Table of Contents
** Minutes
What is a perpetual inventory system?
Perpetual vs. periodic inventory systems
5 advantages of perpetual inventory systems
How do perpetual inventory systems work?
Formulas used in perpetual inventory methods
Inventory is the lifeblood of your business. You need enough inventory in stock to keep up with customer demand, but not so much that you are overpaying on storage costs. That’s why it’s crucial to have an inventory system in place, so you know exactly how much inventory you have at any given time.
The perpetual inventory system is a reliable way to keep track of inventory in real-time. In this article, we’ll share what a perpetual inventory system is and how it works.
What is a perpetual inventory system?
A perpetual inventory system is a system used to track and record stock levels, in which every purchase and sale of stock is logged automatically and immediately. In this system, every time a transaction takes place, software records a change in inventory levels in real-time.
Thanks to recent advancements in technology, it is much easier for brands of all sizes to implement a perpetual inventory system. Brands can collect data through IOT devices such as RFID tags, barcoding scanners, and sensors, and access real-time data through cloud-based software solutions for constant visibility.
What is perpetual inventory?
Perpetual inventory is an accounting method in which a business continuously tracks its inventory levels in real-time, rather than just counting inventory at the end of a financial period. This method makes more precise inventory counts available to a business at all times.
Perpetual inventory is distinguished from a perpetual inventory system, which usually refers to the software or program that executes the perpetual inventory accounting method.

Perpetual vs. periodic inventory systems
Periodic and perpetual inventory systems are two different inventory tracking methods that ecommerce businesses use to track and monitor stocked goods. The perpetual inventory system is more advanced and used more often than a periodic system.
A perpetual inventory control system tracks inventory in real time and centralises inventory data. Inventory data is available to all parts of the system to forecast sales trends, calculate reorder points, and source items that are currently out of stock.
A periodic inventory system is kept up to date by a physical count of goods on hand at specific intervals to calculate COGS using inventory valuation methods such as FIFO, LIFO, and weighted averages. With a periodic inventory system, retailers calculate current inventory counts at the end of an accounting period or financial year and only then report on it.
5 advantages of perpetual inventory systems
A perpetual inventory system has a lot of advantages for ecommerce businesses of all sizes. Not only does it help track inventory data in real-time, but it also helps eliminate labour costs and human error. Let’s look at why ecommerce businesses choose to use a perpetual inventory system.
Records data in real-time
A perpetual system records inventory updates and movements as they happen. This means you can trust your inventory counts to be accurate at all times.
“ShipBob’s reporting is very robust and meets all of our needs. We get visibility into receiving, order volume, SKU availability – everything from inbounds and inventory transactions to individual order statuses (whether it’s on hold, in processing, an exception order, and other detailed descriptions). All this data is real-time, meaning that we’re always seeing the most accurate, up-to-date information. Having this real-time data is crucial for my team, so the fact that there’s not hours of lag time waiting for data to update is huge.”
Ryan Steffenson, Senior Manager, Channel Operations at Tonies
Provides a detailed paper trail
A perpetual inventory system tracks inventory movements and interactions throughout your ecommerce supply chain. This data will give you more insights about bottlenecks in your procedures, so you find ways to optimise your supply chain.
Decreases inventory management costs
With real-time updates, inventory holding costs and inventory replenishment are controlled and minimised. Since perpetual inventory systems automate many processes that would be manual, it can save on labour costs.
Calculates end-of-year inventory balance
Since a perpetual inventory system accounts for inventory continuously, your end-of-year inventory balance is calculated instantaneously when the year ends. This helps to make sure you have accurate inventory numbers to report on for accounting purposes.
Forecasts demand more accurately
A real-time inventory system makes forecasting demand simple. Historical inventory and sales data can be used to predict future sales cycles and ensure that you have an optimal amount of inventory during different times in the season, such as the holidays.
“When we started selling in the US, we were still adjusting to the learning curve and didn’t fully understand how seasonal our business would become. In working with ShipBob, they were able to help us understand what had happened with similar clients in the toy space during the holidays in previous years so that we were prepared for what’s to come.
Now we know that our business is extremely seasonal – and when combined with our brand’s 50% year-over-year growth rate, it makes maintaining fulfilment a really hard challenge to tackle. But we can just send ShipBob’s team forecasts for order volume, and ShipBob makes sure there’s enough manpower to handle it without us having to manage anything.”
Molly Noonan, Senior Manager, Supply Chain at Tonies
How do perpetual inventory systems work?
A perpetual inventory system works by updating inventory counts continuously as goods are bought and sold. This inventory accounting method provides a more accurate and efficient way to account for inventory than a periodic inventory system. Here is a step-by-step overview of how this type of inventory system works.
Step 1: Point-of-sale system updates inventory levels
Whenever a product is sold, the inventory management system attached to the POS (point-of-sale) system immediately applies the debit to the main inventory across all sales channels. Barcodes or RFID (radio-frequency identification) scanners make this process quick and easy.
For example, let’s say you run a business that sells scented candles. A customer purchases 3 vanilla-scented candles (in other words, 3 units of a single SKU) for $10.00 per candle, or $30.00 total.
When a warehouse picker picks each unit, the picker scans each candle’s barcode. As soon as each barcode is scanned, your perpetual inventory system’s software decreases the overall inventory count for that SKU by 3.
With the perpetual inventory system, sales to customers also trigger two accounting journal entries on your income statement, and two on your balance sheet.
On your income statement, the amount of money the customer pays for the items — in this case, $30.00 — is recorded as a credit to revenue. On your balance sheet, this same amount is logged as a credit to accounts receivable or cash.
Step 2: Cost of goods sold is updated automatically
Whenever a product is sold or received, the cost of goods sold (COGS) gets recalculated.
Continuing the example above, we’ll assume that the COGS for each vanilla-scented candle (which factors in expenses like raw materials, warehouse labour, and overhead expenses) is $5.00 per unit. Every time a candle is scanned, $5.00 is added to your business’s overall COGS — meaning that after scanning 3 candles, the COGS increased by $15.00.
This $15.00 should be recorded in two more accounting journal entries. On your income statement, $15.00 is recorded as a debit to COGS. On your balance sheet, this same amount is credited to your inventory.
Step 3: Reorder points are adjusted frequently
Based on historical data, a perpetual inventory system will automatically update reorder points as sales increase or decrease to keep an optimal level of inventory at all times.
Following the previous example, let’s say your store offers a special holiday-themed candle, and for the past 4 years, sales for that candle have always risen in Q4.
A perpetual inventory system will learn from the sales data of the past 4 years, and automatically raise your reorder threshold from 25 units to 50 units. This way, you can reorder stock sooner than you normally would and prevent stockouts.

Step 4: Purchase orders are automatically generated
Whenever an item or SKU hits its reorder point, the system generates a new purchase order and sends it to your supplier with no human intervention.
For example, sales for your holiday-themed candle increase rapidly in Q4, just as you predicted. As soon as you have just 50 units of that candle left in stock, your perpetual inventory system will automatically generate a new purchase order for 500 more candles (to be bought at $3.00 apiece) and send it to your supplier.
This purchase transaction triggers another journal entry, this time only on your balance sheet. In this example, a total of $1,500 (500 units x $3.00 each) should be recorded as a debit to inventory, and a credit to either accounts payable or cash.
Step 5: Received products are scanned into inventory
When inventory is sent to your warehouse, a warehouse employee will scan product using a warehouse management software (WMS), so they appear in your inventory management dashboard and make them available for purchase on all or select sales channels.
In our example, let’s say the purchase order goes through, and after a week or two your supplier’s shipment of 500 candles arrives at your warehouse.
As your warehouse employees go through the receiving process, each unit is checked for quality and scanned with a barcode scanner before it’s moved to warehouse storage. As soon as a unit is scanned, the perpetual inventory system automatically increases the inventory count for that SKU by 1. Once all 500 units are scanned, the inventory count should have increased by 500.

Formulas used in perpetual inventory methods
In order to be more precise when ordering inventory items, formulas can be used. There are several formulas business owners can use to keep track of physical inventory counts. Here is a list of our favorites.
EOQ
EOQ, or economic order quantity, is designed to find the optimal order quantity for businesses to minimise certain things like costs, warehousing space, and stockouts.
Formula: EOQ = square root of: [2SD] / H
S = Setup costs (per order, generally including shipping and handling)
D = Demand rate (quantity sold per year)
H = Holding costs (per year, per unit)
Finished goods
Finished goods inventory refers to the stock available to customers for purchase that can be picked, packed, and kitted. With the finished goods inventory formula, sellers can calculate inventory cost.
Formula: (COGM – COGS) + Value of Previous Year’s Finished Goods
FIFO
FIFO (first in, first out) is an inventory valuation method that sells the goods purchased first before goods purchased later. In theory, this means the oldest inventory gets shipped out to customers before newer inventory.
LIFO
LIFO (last in, first out) is an inventory valuation method that uses the cost of the most recent products purchased to calculate the cost of goods sold (COGS), while older inventory value is considered ending inventory on a balance sheet.
Weighted average cost
Weighted average cost is an accounting system that uses a weighted average to determine the amount of money that goes into COGS and inventory.
Formula: Cost of goods available for sale / Total number of units in inventory
ShipBob offers the ultimate inventory management software
A perpetual inventory system is a great choice for fast-growing ecommerce businesses. In addition to a lower likelihood of discrepancies and stronger stock control, brands can centralise inventory management, optimise stock levels, and much more.
As an expert fulfilment partner, ShipBob’s technology features built-in perpetual inventory management capabilities. Through ShipBob’s dashboard, ecommerce brands can achieve real-time visibility into inventory levels and track SKUs as they are received, stowed, picked, packed, and shipped to customers.
ShipBob’s fulfilment technology comes with built-in inventory management tools, including demand forecasting, order management, and data and analytics. Merchants can track SKU velocity, track storage costs, and even calculate the ideal distribution of inventory across ShipBob’s network.

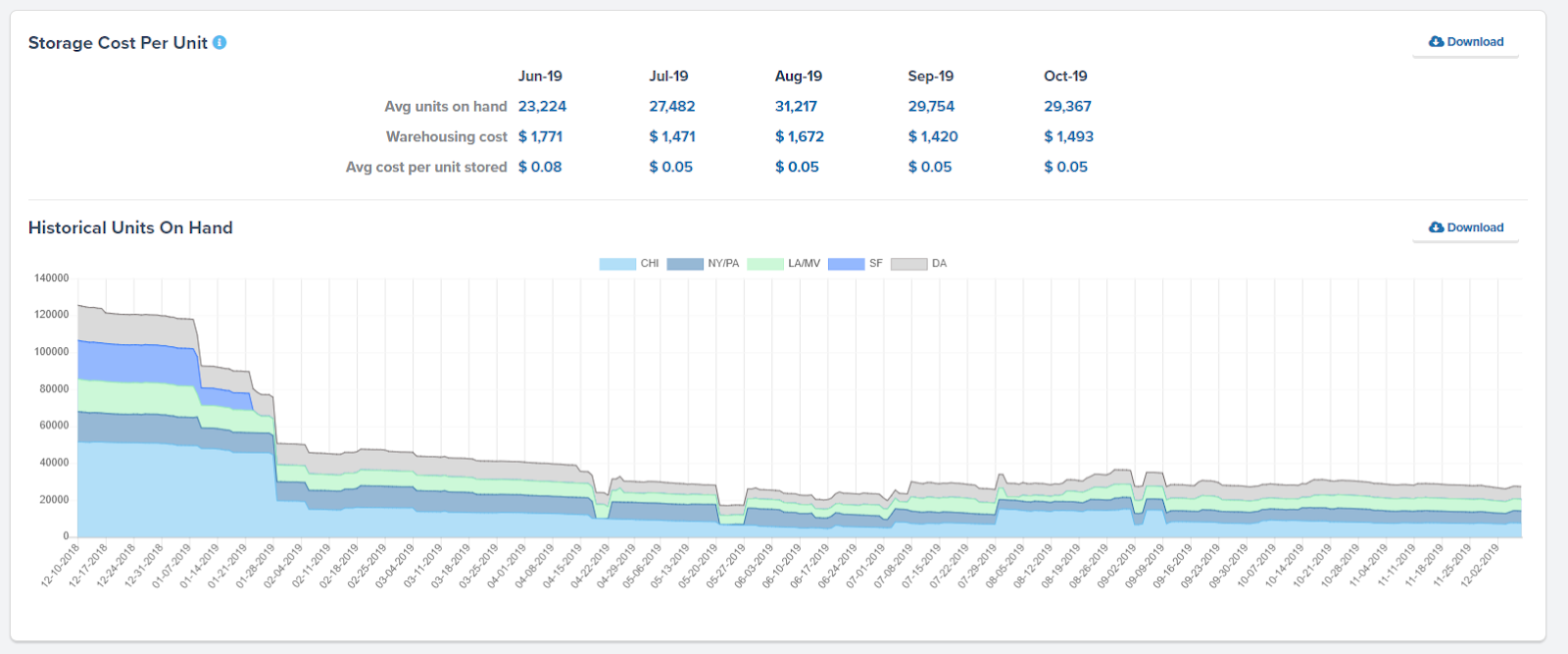

To learn more on how ShipBob can support your ecommerce business, click the button below to request information.
Have your own warehouse?
ShipBob has a best-in-class warehouse management system (WMS) for brands that have their own warehouse and need help managing inventory in real time, reducing picking, packing, and shipping errors, and scaling with ease.
With ShipBob’s WMS, brands with their own warehouse can even leverage ShipBob’s fulfilment services in any of ShipBob’s fulfilment centres across the US, Canada, Europe, and Australia to improve cross-border shipping, reduce costs, and speed up deliveries.
Perpetual inventory system FAQs
Below are some of the most common questions about perpetual inventory systems.
Why do companies use perpetual inventory systems?
A perpetual inventory system gives an ecommerce business an accurate view of stock levels at any time without the manual process required for a periodic inventory system. The automation that a perpetual inventory system provides frees up time and capital.
How do you record inventory in a perpetual system?
In a perpetual inventory system, inventory is recorded any time inventory is purchased and received by a merchant or sold to customer. Inventory levels are then either increased or decreased to reflect the changes in real-time, so inventory counts are constantly being adjusted.
How does a perpetual inventory system impact financial statements?
Purchasing inventory from a supplier or manufacturer triggers a journal entry on your balance sheet, the amount spent should be recorded as a credit to inventory and either a credit to accounts payable or a debit to cash.
Sales to customers trigger two accounting journal entries on your income statement, and two on your balance sheet. On your income statement, the amount of money the customer pays for the items is recorded as a credit to revenue. On your balance sheet, this same amount is logged as a credit to accounts receivable or cash.
Which industries benefit most from using a perpetual inventory system?
Most businesses could benefit from perpetual inventory systems, but it may be particularly helpful for brands that experience high inventory turnover, reorder inventory frequently, or are looking to achieve more accurate data and demand forecasts.
What’s the difference between perpetual inventory and book inventory?
Book inventory refers to the amount of stock a business has on hand, according to accounting records. It is not necessarily the same as actual inventory (which is the true amount of stock that a business has on hand), as inventory may be damaged, lost, stolen, or otherwise over- or under-counted in the books.
Perpetual inventory systems help keep your book inventory more accurate, as you’re less likely to miss transactions, damage, lost inventory, and other inconsistencies more quickly with detailed, real-time records.