Table of Contents
** Minutes
Core functions of warehousing every brand should know
Security and risk mitigation strategies in warehousing functions
How technology powers each warehousing function
How ShipBob optimises warehouse functions for ecommerce brands
Many dismiss warehousing simply as storage.
But they couldn’t be more wrong: a warehouse is a dynamic hub of activity that is the foundation of the entire ecommerce order fulfilment process.
From receiving and storing inventory to picking, packing, and shipping orders, there are critical functions that occur within the warehouse that keep your supply chain running smoothly.
And when optimised, these warehouse processes don’t just improve internal efficiency, they reduce costs, speed up deliveries, and build customer loyalty.
In this guide, we’ll unpack the essential functions every ecommerce warehouse must master, along with best practices, real-world examples, and technology tips to help.
What are warehouse functions?
Warehouse functions are the essential activities performed within a warehouse that ensure products move efficiently through the supply chain. These functions form the backbone of logistics operations, particularly for ecommerce businesses that rely on seamless product flow to meet customer expectations.
From the moment goods arrive at a warehouse to the time they’re shipped out to customers, various warehouse functions maintain inventory accuracy, enable order fulfilment speed, and boost overall operational efficiency. When these functions are well-managed and optimised, businesses can better control costs, improve customer satisfaction, and ultimately drive growth.
However, managing warehouse functions is no simple feat. Ecommerce businesses must navigate a complex web of processes, from receiving and storing inventory to picking, packing, and shipping orders. Each function requires logistics technology and tools, as well as careful planning, execution, and oversight to avoid costly errors and delays.
Warehousing functions vs. overarching warehousing operations
It’s important to note that while specific functions like receiving, storing, and picking are key components of warehouse management, they are distinct from the broader scope of warehousing operations. Total warehousing operations encompass a wide range of activities that ensure the inner workings of the warehouse are running smoothly and warehouse functions can occur seamlessly. Common warehousing operations include:
- Facility management and maintenance
- Workforce planning and labour allocation
- Quality control and inventory auditing
- Safety and compliance management
Understanding the distinction between individual warehouse functions and overall operations is crucial for businesses looking to optimise their supply chain. By recognizing the unique challenges and requirements of each function, companies can better allocate resources, implement targeted solutions, and measure performance at a granular level.
At the same time, understanding how warehousing operations impact warehouse functions is important to identify opportunities for process improvement. For example, adding additional warehouse associates during the holidays can have a positive impact on fulfilment speeds. The increased number of associates means more orders can be processed in the same amount of time, resulting in greater productivity during peak season.
Core functions of warehousing every brand should know

Warehousing is not a single, monolithic process – it’s a complex system of interconnected functions that must work together seamlessly to keep products flowing efficiently from suppliers to customers.
In the fast-paced world of ecommerce, these functions have evolved to meet the unique demands of online selling, such as rapid order processing, high inventory turnover, and the need for scalability during peak periods. Let’s take a closer look at the six primary warehouse functions that every ecommerce brand should master.
1. Receiving
Receiving is the first step in the warehousing process, which sets the stage for all subsequent functions. When inbound shipments arrive at the warehouse, associates must carefully unload, inspect, and verify the contents against shipping documents, such as warehouse receiving orders (WROs), to ensure accuracy and prevent discrepancies.
Best practices for warehouse receiving include:
- Scheduling deliveries in advance to avoid congestion at warehouse docks and optimise labour allocation.
- Using barcode scanners or RFID technology to quickly and accurately record inbound inventory.
- Conducting thorough inspections to confirm product quantities are the same as outlined in the shipping documents and identify any damaged or defective products.
- Promptly updating inventory counts within the warehouse management system (WMS) to reflect new stock levels.
At ShipBob, associates utilise our proprietary WMS and WROs documentation to streamline receiving and ensure pinpoint accuracy. By leveraging advanced technology and rigorous quality control measures, ShipBob helps ecommerce brands maintain precise inventory counts from the moment products arrive at the fulfilment centre.
2. Storing
Once products have been received and inspected, they must be properly stowed within the warehouse. Effective storage strategies involve organising inventory by a variety of factors such as SKU, product type, or demand frequency and using appropriate storage systems like pallet racking, shelving, or bin storage.
Ultimately, a well-designed storage system sets the stage for efficient picking and helps to minimise errors, damage, and stockouts. By leveraging best practices and technology solutions, ecommerce brands can optimise their storage processes to drive efficiency and protect their inventory investment.
3. Picking
Picking is the warehouse process of retrieving products from their storage locations to fulfil customer orders. As one of the most labour-intensive and time-consuming warehouse functions, picking is a prime target for optimisation efforts.
Effective picking strategies include:
- Implementing batch, zone, or wave picking methods based on order volume and warehouse layout.
- Using pick lists and mobile devices to guide pickers through the most efficient routes.
- Leveraging technology like voice-directed picking or pick-to-light systems to increase speed and accuracy.
- Strategically stowing frequently picked items closer to pack stations to minimise the destination between pick and pack.
With advanced picking technologies and data-driven strategies, ShipBob helps merchants streamline order fulfilment to get orders out the door and into the hands of your customers faster.
4. Packing
Once orders have been picked, they are packed and prepared for shipment. Efficient packing workflows are crucial for ensuring orders are shipped quickly and securely.
Packing stations should be strategically set up with all necessary materials within easy reach, such as boxes, mailers, tape, labels, and dunnage. This minimises the time packers spend searching for supplies and maximises their productivity.
Choosing the right packaging materials is also essential. When packing orders there are a number of factors to consider, including product fragility, size, and weight, as well as sustainability and branding requirements. Properly sized packaging not only protects products during transit but also ensures accurate dimensional weight (therefore helping brands avoid unnecessary charges from couriers).
In addition to practical considerations, packaging also plays a key role in the customer experience. The unboxing process is a prime opportunity to reinforce your brand and create a positive impression. Custom packaging, branded inserts, and personalised gift notes can go a long way in delighting customers and encouraging repeat purchases. These options showcase your brand, provide marketing information, and create a memorable unboxing experience.
To further enhance the customer experience, many ecommerce businesses opt for value-added services like kitting. Kitting involves pre-assembling multiple SKUs into a single unit, which can be an effective strategy for product bundles, subscription boxes, or promotional offerings.
ShipBob’s Customisation Suite offers a range of value-added services to help ecommerce brands elevate branded unboxing experience. In addition to customisation options, ShipBob can handle kitting projects of any size or complexity, from simple two-item bundles to multi-product subscription boxes with variable contents. By outsourcing fulfilment to ShipBob, merchants can achieve a polished and professional packing process that will delight customers.
5. Shipping
Shipping is the pivotal function where packed orders leave the warehouse and begin their journey to customers. Efficient shipping requires precise coordination between warehouse operations and transportation couriers to ensure timely deliveries and satisfied customers.
Effective shipping practices include:
- Selecting appropriate couriers (either major couriers like FedEx, UPS, and DHL or smaller, regional couriers) based on factors like shipping cost, speed, geographic reach, and reliability.
- Generating accurate shipping labels and documentation to minimise errors, streamline courier processing, and ensure compliance with international shipping regulations, when necessary.
- Implementing rate-shopping technology to automatically select the most cost-effective and timely shipping options for each order.
- Providing customers with tracking updates, providing them with visibility into their order’s delivery status, and enhancing their overall experience.
ShipBob leverages its extensive network of strategically located fulfilment centres to provide ecommerce brands with optimised shipping solutions. By positioning inventory closer to customers, ShipBob ensures shorter transit times, lower shipping costs, and increased delivery reliability, ultimately helping merchants build customer loyalty through consistently excellent shipping experiences.
In the US, brands can utilise ShipBob’s Inventory Placement Program (IPP) to automatically distribute, balance, and replenish inventory across the country. Additionally, ShipBob has a network of over 60 fulfilment centres around the globe so brands can place inventory in multiple markets to reach international customers more seamlessly and minimise duties and taxes.
6. Returns management
Returns management—or reverse logistics—is an essential warehousing function focused on efficiently handling returned products. With ecommerce return rates averaging between 15% to 30%, optimising returns management is crucial for maintaining customer trust, minimising costs, and recovering value from returned inventory.
Key strategies for effective returns management include:
- Streamlining the returns intake process by clearly communicating return policies on your website and sales channels, providing prepaid return labels, and implementing easy-to-use returns portals.
- Conducting thorough inspections upon return to assess product condition, determine eligibility for resale, refurbishment, recycling, or disposal, and promptly updating inventory records accordingly.
- Analising return data to identify product quality issues, inaccurate product listings, or packaging shortcomings, enabling proactive corrective actions.
- Speeding up customer refunds or exchanges to maintain trust, enhance customer satisfaction, and encourage future purchases.
- Emphasizing exchanges to recoup a portion of the original sale while satisfying the customer.
ShipBob simplifies returns management for ecommerce brands by offering streamlined returns processing through their fulfilment centres. With dedicated returns handling protocols, ShipBob ensures rapid inspection, accurate restocking (including return-to-sender (RTS) restock options), and real-time inventory updates, enabling merchants to efficiently manage returned merchandise, reduce losses, and deliver exceptional customer service at every touchpoint.
Check out ShipBob's Warehouse Management System (WMS)
ShipBob's WMS helps your warehouse reduce picking errors, manage inventory in real time, and fulfill orders faster.
Security and risk mitigation strategies in warehousing functions
Ensuring the security of your inventory and mitigating potential risks is critical for protecting your bottom line and maintaining business continuity. The level of security required will depend on the type and value of the products being stored, but every warehouse should have measures in place to safeguard against theft, damage, and non-compliance.
Safeguarding goods and minimising damage
Physical security is the first line of defense in protecting your inventory. This includes surveillance systems, access control measures, and trained security personnel to monitor the premises. Implementing strict inventory control procedures, such as regular cycle counts and real-time tracking, can also help prevent shrinkage and identify potential issues early on.
Proper handling techniques of fragile items or hazardous materials are essential to minimise damage and to ensure associate safety .. This may involve specialized equipment, staff training, and designated storage areas within the warehouse.
At ShipBob, stringent security protocols are implemented across all fulfilment centres to protect merchant inventory. From 24/7 surveillance and access control to regular inventory audits and ICQA, ShipBob takes a comprehensive approach to safeguarding your products.
Ensuring product safety and regulatory compliance
Brands that sell products in the food, supplement, pharmaceutical, or electronics categories should prioritize storing their inventory in warehouses with climate controls. Climate control is a critical consideration for brands storing sensitive products, as maintaining proper temperature and humidity levels preserves product quality and ensures compliance with industry regulations.
Compliance with industry-specific regulations, such as FDA or USDA guidelines, requires meticulous record-keeping and traceability measures. This includes lot tracking capabilities to facilitate swift product recalls if necessary.
ShipBob’s fulfilment centres are equipped to handle a wide range of regulated products, with specialized capabilities for temperature-sensitive goods and hazardous materials. By partnering with a third-party logistics (3PL) provider like ShipBob, ecommerce brands can ensure their products are stored and handled in full compliance with all relevant regulations.
ShipBob has solutions for brands that require climate controls and warehouse compliances such as GMP and GFSI, lot tracking, FIFO or FEFO inventory management, and more.
How technology powers each warehousing function
In today’s fast-paced ecommerce landscape, technology has become the key enabler of efficient, accurate, and scalable warehouse operations. From inventory management software to automation tools and AI-powered analytics, digital solutions are transforming every aspect of the warehousing process.
By leveraging data-driven insights and real-time visibility, businesses can optimise their warehouse functions for maximum performance and profitability. The ROI of technology investments will vary depending on the size and complexity of the operation, but the benefits are clear: streamlined processes, real-time data, reduced errors, and the ability to scale quickly to meet demand.
Warehouse management systems (WMS)
A warehouse management system (WMS) is the backbone of modern warehousing operations. This software platform provides end-to-end visibility and control over warehouse functions, including inventory, orders, and labour, enabling businesses to optimise every aspect of the fulfilment process.
Core WMS functionality includes real-time inventory tracking, order management, and staff allocation. Advanced systems also offer seamless integration with popular ecommerce platforms like Shopify and Amazon, as well as robust reporting and analytics capabilities to drive continuous improvement.
ShipBob’s proprietary WMS is designed specifically for the needs of ecommerce businesses, providing merchants with real-time visibility into warehouse activities and inventory levels. With ShipBob, brands can easily monitor performance, identify trends, and make data-driven decisions to optimise their operations.
Automation tools and AI
Physical automation solutions, such as conveyor systems, sortation equipment, and robotics, can significantly boost warehouse productivity and accuracy. These tools streamline repetitive tasks, reduce manual handling, and minimise the risk of errors, particularly during peak periods when order volumes are high.
Artificial intelligence (AI) and machine learning (ML)algorithms are also transforming warehouse operations by enabling more accurate demand forecasting, intelligent route optimisation, and predictive maintenance. By leveraging AI insights, businesses can proactively address potential issues and optimise their resources for maximum efficiency.
The key to successful automation is striking the right balance between technology investment and labour. This looks different for businesses at different growth stages. For some, this may involve a phased approach, gradually incorporating automation tools in their own warehouse as order volumes and complexity increase. For others, this may mean working with a fulfilment provider like ShipBob that has access to best-in-class technology and automations.
Cloud-based and mobile visibility
Cloud-based warehouse management systems offer significant advantages over traditional on-premise solutions, most notably in terms of scalability, accessibility, and real-time data synchronization. With a cloud-based WMS, businesses can easily manage their inventory and operations from anywhere, at any time, since information is not saved locally on specific machines or hardware.
Mobile devices are also transforming the way warehouse staff work, enabling them to access and update information on the go. From receiving and putaway to picking and packing, mobile solutions streamline every step of the process, reducing manual data entry, and increasing overall efficiency.
For ecommerce brands, cloud-based and mobile visibility tools are essential for keeping customers informed about order status and inventory availability. ShipBob’s intuitive dashboard, for example, provides merchants with instant access to real-time inventory levels, order tracking, and performance metrics, empowering them to make informed business decisions.
How ShipBob optimises warehouse functions for ecommerce brands
ShipBob is a best-in-class global fulfilment platform that specializes in omnichannel ecommerce order fulfilment. ShipBob offes a full suite of solutions to help brands optimise their fulfilment operations and exceed customer expectations.
With a network of fulfilment centres across the US, Canada, Europe, and Australia, ShipBob enables merchants to streamline their logistics, reduce costs, ship orders quickly, and scale efficiently.
In addition to its core fulfilment services, ShipBob offers a range of value-added capabilities to help ecommerce brands elevate their customer experience and grow their business.
ShipBob’s industry-leading WMS

At the core of ShipBob’s offering is a proprietary warehouse management system that integrates seamlessly with popular ecommerce platforms like Shopify, Amazon, Target, and Walmart.
ShipBob’s WMS is designed specifically with ecommerce merchants in mind, making it a top choice for brands looking to optimise their warehouse operations.
This powerful system offers the same advanced functionality used in ShipBob’s own fulfilment centres, enabling businesses to manage their inventory, orders, and shipping with ease.
With ShipBob’s WMS, merchants can access real-time inventory tracking, set up automated reorder points, and optimise product allocation across multiple storage locations. The system also streamlines key warehouse functions like receiving, putaway, and picking, with built-in tools for reducing errors and improving efficiency.
Real-time inventory updates and demand fluctuations
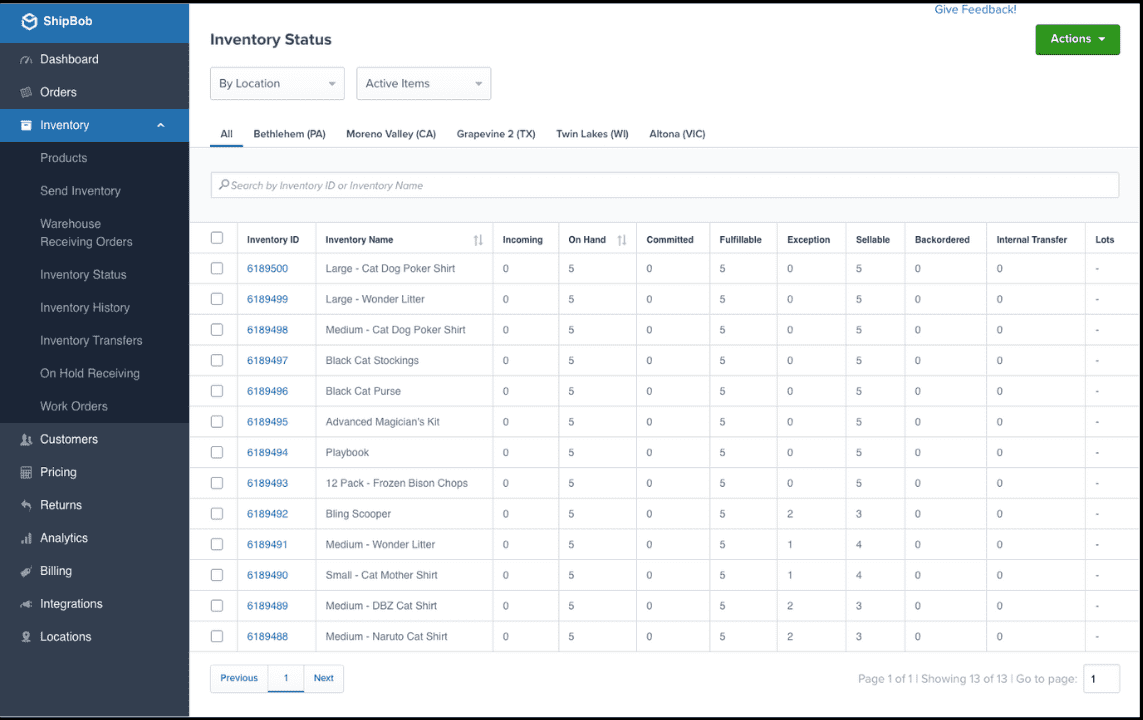
One of the biggest challenges in ecommerce is managing inventory levels to avoid stockouts and overstock situations. ShipBob’s technology provides real-time visibility into inventory levels, enabling merchants to track their stock across multiple fulfilment centres and sales channels.
This level of transparency is critical for managing demand fluctuations, particularly during peak seasons or promotional periods. With ShipBob, brands can easily monitor inventory levels, set up automatic reorder points, and even use historical data to forecast future demand.
By leveraging ShipBob’s data and analytics tools, merchants can make informed decisions about purchasing, product allocation, and supplier relationships. This not only helps to prevent stockouts and overstocking but also frees up working capital and improves overall supply chain efficiency.
Faster delivery and better customer experiences
In today’s fast-paced ecommerce landscape, customers expect nothing less than fast, reliable shipping. ShipBob’s distributed fulfilment network is designed to help merchants meet these expectations, with strategically located centres that enable 2-day shipping in the contiguous US.
By storing inventory closer to end customers, ShipBob helps brands reduce shipping costs, speed up delivery times, and improve the overall customer experience. This not only leads to higher satisfaction and repeat purchase rates, but also helps to reduce cart abandonment and boost conversions.
ShipBob’s technology also provides customers with real-time order tracking and proactive communication at every stage of the fulfilment process. This level of transparency helps to build trust and loyalty, turning one-time buyers into lifelong brand advocates.
Get started with ShipBob
Interested in leveraging ShipBob’s fulfilment solutions? Fill out the form to get a customised quote.
Warehouse functions FAQs
Here are some frequently asked questions about warehouse functions and how they impact ecommerce businesses and fulfilment worldwide.
How do conveyor systems and robotics improve warehouse efficiency?
Conveyor systems and robotics can significantly boost warehouse efficiency by increasing throughput, reducing errors, and minimising manual labour. Conveyors automate the movement of goods between different areas of the warehouse, such as from receiving to storage or from picking to packing. This reduces the time and effort required for workers to transport items manually.
Robotics, such as autonomous mobile robots (AMRs) and robotic picking arms, can further enhance efficiency by assisting with tasks like retrieving items from storage, transporting goods, and even picking and packing orders. These automation technologies not only improve speed and accuracy but also reduce physical strain on workers, leading to a safer and more ergonomic work environment.
What is the difference between a fulfilment centre and a bonded warehouse?
A fulfilment centre is a type of warehouse that focuses on processing and shipping orders directly to customers (DTC). These facilities are designed to handle a high volume of individual orders and are optimised for rapid order processing, picking, packing, and shipping.
In contrast, a bonded warehouse is a secure storage facility that holds imported goods before duties and taxes are paid. This allows importers to defer payment of duties until the goods are sold or removed from the bonded warehouse for consumption. Bonded warehouses are primarily used for B2B transactions and are subject to strict customs regulations.
How do I choose the right WMS for my small vs. growing ecommerce business?
When selecting a warehouse management system (WMS) for your ecommerce business, consider your current needs and future growth plans. For small businesses, essential features include real-time inventory tracking, order management, and basic reporting capabilities. The WMS should integrate seamlessly with your ecommerce platform and be user-friendly for your staff.
As your business grows, you may require additional features such as demand forecasting, warehouse labour management, advanced analytics, and more robust integration capabilities. No matter where your business is in your in-house fulfilment journey, ShipBob’s WMS can accommodate your increasing order volume and inventory levels, streamline order fulfilment in your own facility, and give you real-time data at your fingertips.
What safety and environmental controls are essential in modern warehousing?
Modern warehouses must prioritize safety and environmental controls to protect workers, products, and the environment.
Essential safety measures include:
- Ergonomic practices, such as teaching proper lifting techniques and thoughtful workstation design
- Regular safety training and the use of personal protective equipment (PPE)
- Environmental controls, such as temperature and humidity regulation, for storing sensitive products like food, pharmaceuticals, and electronics
- Adequate ventilation and air filtration systems to maintain air quality and prevent the buildup of dust and pollutants
- Compliance with regulatory standards such as OSHA and EPA
How can ShipBob help optimise my warehouse functions?
ShipBob is a leading ecommerce fulfilment provider that specializes in optimising warehouse and fulfilment functions for online businesses. With a global network of strategically located fulfilment centres and a proprietary technology platform, ShipBob streamlines the entire fulfilment process, from receiving and storage to picking, packing, and shipping.
By partnering with ShipBob, ecommerce businesses gain access to a powerful WMS that provides real-time visibility into inventory levels, order status, and performance metrics. And, ShipBob’s distributed fulfilment network enables businesses to store inventory closer to their customers, reducing shipping costs and delivery times.