Table of Contents
** Minutes
The importance of knowing your beginning inventory
Where and when to use beginning inventory?
Beginning inventory formula: what you’ll need
How to calculate beginning inventory
Beginning inventory calculation examples
Beginning inventory calculation examples
How to find beginning inventory when using multiple warehouses
If you start out a quarter with more inventory than when you started the previous quarter, is it a good thing or a bad thing?
It could mean you stocked up in preparation for a big sale or rise in demand. Or, it’s an indication that you have more inventory than you can sell.
If you start out with less inventory than the period prior, it could mean you sold a lot of your stock — congratulations! Or, it’s a sign you’re facing issues at some link in your retail supply chain and don’t have enough stock available.
Inventory fluctuations happen for different reasons and are very normal. That’s why calculating your beginning inventory is so important for financial stability, demand forecasting, inventory calculations, updating your balance sheets, and much more.
Let’s jump into what beginning inventory is and how to easily calculate it.
What is beginning inventory?
Beginning inventory, or opening inventory, is the total value of items a business has in stock that are ready to sell or be used at the start of an accounting period. This amount of inventory should equal the same amount of ending inventory from the prior accounting period.
It’s important for brands to track beginning inventory so they can manage stock levels and on-hand inventory, and make informed decisions about purchasing more inventory.
Beginning inventory looks different for manufacturers and for retailers. For a manufacturer, beginning inventory may include raw materials, items that are in production, and finished goods. However, a retailer’s beginning inventory is made up of products that are available for consumers to purchase.
Formula to calculate beginning inventory (+ what you’ll need)
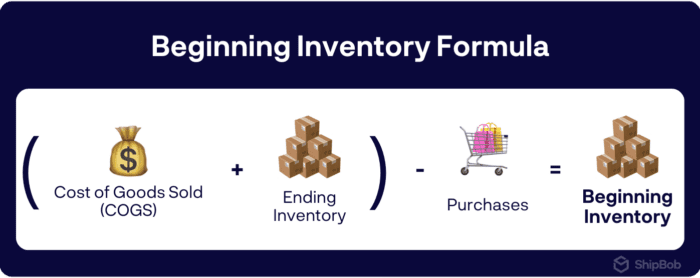
Before you begin calculating beginning inventory, you’ll need to find the values to solve the equation. Whether you’re using a perpetual inventory system or the periodic inventory method, the following supporting formulas often coincide with calculating the beginning inventory of an accounting period.
COGS
To calculate the cost of goods sold (COGS) at the end of an accounting period, you can use the records from your previous accounting period.
Cost of Goods Sold (COGS) =
(Beginning Inventory + Purchases) – Closing Inventory
Ending inventory from prior financial period
Your accounting records from the prior financial period help you determine where you left off. In other words, your ending inventory from Q3 is your beginning inventory in Q4.
If this is your first time calculating ending inventory, you will need to determine how much new stock was purchased and sold in a period of time.
Ending Inventory = Beginning Inventory + Net Purchases – COGS
Note: Choosing the right inventory valuation method for your ending and beginning inventory is crucial for maintaining a financially strong balance sheet. Inventory can be valued using methods such as LIFO (last-in first-out), FIFO (first-in first-out), and even inventory weighted average.
Now you can calculate beginning inventory in four easy steps.
Beginning Inventory Formula = (COGS + Ending Inventory) – Purchases
- Step 1. Determine the COGS with the help of your previous accounting period’s records. To calculate the cost of goods sold at the end of an accounting period, you can use the records from your previous accounting period. Find the COGS formula above.
- Step 2. Next, multiply your ending inventory balance with how much it costs to produce each item, and do the same with the amount of new inventory.
- Step 3. Calculate the ending inventory and cost of goods sold.
- Step 4. Finally, subtract the amount of inventory purchased from your result, and you’ll get your beginning inventory.
The importance of knowing your beginning inventory
There are various benefits to knowing your beginning inventory. Consider the following:
- Transparency
Your beginning inventory tells you how much inventory you have to work with, and how much inventory you need to order to avoid stockouts. Beginning inventory can also be used to calculate how much merchandise was sold during a given period.
- Improved forecasting
When you know how much inventory you have at the beginning of an accounting period, you can make smarter purchasing decisions based on your forecasted demand for the remainder of that period. This is especially helpful prior to peak season or to prepare for seasonal demand.
- Better inventory management
By knowing your beginning inventory at the start of an accounting period, you’re better able to identify inventory that is at risk of becoming “dead stock” by keeping track of the inventory that’s at risk of being no longer sellable. Additionally, you’ll have a better understanding of your inventory levels so you can avoid stockouts.
- Helps determine COGS
In order to calculate your cost of goods sold, or COGS, you need to know your beginning inventory. Your COGS is the amount of products sold in a period of time, minus beginning inventory. Understanding both of these metrics allows you to know the cost of producing and selling your products.
How to value inventory
Choosing the right inventory valuation method for your ending and beginning inventory is crucial for maintaining a financially strong balance sheet. There are multiple valuation methods that can be used depending on business size and needs. Here are 4 inventory valuation methods.
1. Weighted average cost (WAC)
Also known as the average cost method, this method of valuation is good for businesses that ship packages of similar sizes. The formula is as follows:
Weighted Average Cost = Cost of Goods Available for Sale / Total Units in Inventory
2. Specific identification method
This tends to be the most accurate method since every single item is tracked individually. This method is best for businesses with products that vary greatly in size and value. There is no formula for this method, all you need to do is tag each and every item with its purchase value and incurred value until it is sold.
3. First-in first-out (FIFO)
FIFO is a commonly used valuation method since it is simple to use. As the name implies, inventory that is produced first will seemingly be sold first. With this method you can calculate value based on the inventory you have on hand.
4. Last-in first-out (LIFO)
LIFO is less common and not the most practical since most businesses wouldn’t want to sell their newest products first. However, there are tax advantages. The end result of LIFO means higher COGS and lower balance of remaining inventory, which means less taxes, which means more cash flow.
Where and when to use beginning inventory?
Beginning inventory is an important aspect of inventory accounting that you’ll need to use to measure and track your business’s performance.
Here are common uses for beginning inventory.
To identify shrinkage
Beginning inventory can help identify any possible inventory shrinkage.
Because beginning inventory is reconciled with the last period’s ending inventory, you can determine whether there are discrepancies like inventory loss or tracking and recording errors.
When you regularly track your beginning inventory (as well as ending inventory), you have a reference point of appropriate stock levels and can hone in on outstanding issues if they arise. These issues may include theft, damage, mismanagement, or reporting inaccuracy.
To determine average inventory for an accounting period
Beginning inventory provides a foundation for tracking, calculating, and understanding the inventory count for an accounting period. Not only does beginning inventory help determine inventory turnover rate, but it can also determine the total amount of products available for sale during the accounting period.
To help understand your business’s financial health
Keeping track of your business’s beginning inventory helps you keep a finger on the pulse of your brand’s financial health, make informed decisions, and drive sustained growth and profitability.
For example, beginning inventory is an important factor when calculating working capital, which are the funds available for operating expenses. Your beginning inventory can help you understand the impact of your inventory cost on available working capital. As a result, you can make decisions about inventory levels and cash flow so you can ensure you have enough stock to meet demand.
Additionally, when you accurately track your inventory, you can keep better balance sheets. Balance sheets are important because they provide a holistic picture of your business’s financial health to investors and stakeholders. Because inventory is often the largest asset an ecommerce business has, it is important accurate inventory documentation is important.
Plus, tracking beginning inventory helps with ecommerce bookkeeping in these other ways:
- Conduct inventory reconciliations and track inventory write-offs when inventory has lost its value and cannot be sold due to damage, theft, loss, or decline in market value.
- Determine future production and reorder quantities so you’re not stuck with too much or too little stock.
- Knowing your beginning inventory helps determine the tax deductions from your stock. Having too large of a beginning inventory, or one that’s too small, can be detrimental for your taxes.
Beginning inventory calculation examples
The easiest way to understand this formula is by walking through an example.
Let’s say you sold 1,000 refrigerators during the last accounting period, and you purchased each one for $500 from the supplier. The cost of goods sold is:
Manufacturing Price x Quantity = COGS
$500 x 1,000 = $500,000
Now, let’s say at the end of the period, you have 500 refrigerators left. This means the ending inventory is worth:
Manufacturing Price x Remaining Quantity = Ending Inventory
$500 x 500 = $250,000
Furthermore, if your business produced or purchased an additional 700 refrigerators in the new year, the cost of the new inventory is:
Manufacturing Price x Quantity = Purchases
$500 x 700 = $350,000
Thus, we can now calculate beginning inventory using the formula:
(COGS + Ending Inventory) – Purchases
($500,000 + $250,000) – $350,000 = $400,000
This means the beginning inventory is $400,000 at the start of the accounting period.
How to find beginning inventory when using multiple warehouses
Large businesses that are shipping a high volume of orders across regions often grow out of centralized inventory, and opt instead for a ‘distributed’ inventory system — in which inventory is divided up and stored in a number of fulfillment centers in various locations. This can help speed up the order delivery process and save on shipping costs.
The good news is that using multiple warehouses doesn’t have to make finding the beginning inventory in each tricky. With a tech-enabled third-party logistics (3PL) company like ShipBob, you can log in to your inventory management system and access real-time inventory counts.
ShipBob’s software fully integrates with your other business systems and gives you direct insight into warehousing and specific information down to the SKU and unit level, from one central dashboard.
You can view not only the beginning inventory numbers and inventory days on hand but inventory forecasting tools, insights into managing inventory turnover, and much more.
Easily manage your inventory with ShipBob
Determining your beginning inventory at the end of each accounting period can be time-consuming if you don’t have a good system for tracking inventory in place.
With ShipBob, you can compute your beginning inventory in no time, without requiring staff to perform an inventory audit or a physical count of the products. ShipBob not only stores products and picks, packs, and kits orders for you, but our inventory management software monitors inventory levels across multiple warehouses, making it an easy choice for fast-growing ecommerce businesses.
View historical inventory levels by changing filters to the date range of your choice, filter down to the product or lot level, view status by channel sold on, and more.
“I felt like I couldn’t grow until I moved to ShipBob. Our old 3PL was slowing us down. Now I am encouraged to sell more with them. My CPA even said to me, ‘Thank God you switched to ShipBob.’ ShipBob provides me clarity and insight to help me make business decisions when I need it, along with responsive customer support.”
Courtney Lee, Founder of Prymal
Connect with a ShipBob fulfillment expert to learn how we make inventory management and order fulfillment even easier for your ecommerce business and get a custom quote.
Have your own warehouse?
If you’re fulfilling orders in-house and need a warehouse management system to help you better track inventory, connect with our team to find out if our WMS is the right solution for you.
Beginning inventory FAQs
Determining your beginning inventory is an important task for ecommerce stores. The following information answers some frequently asked questions about beginning inventory.
What is opening/closing inventory?
Opening inventory, also known as beginning inventory, is the value of inventory that is carried forward from the previous accounting period and is used to compute the average inventory. It also helps to determine cost of goods sold. Closing inventory (also known as ending inventory) is the value of the stock at the end of the accounting period.
What counts as purchases?
In the context of inventory, purchases include raw materials bought for production (also called production inventory), finished goods inventory bought from a supplier, and any equipment acquired throughout the manufacturing process.
How do I calculate COGS?
You can calculate the cost of goods sold from the records documented during your previous accounting period. To calculate this, add the beginning inventory value to purchases during the period, and then subtract the ending inventory from this sum. The result is the cost of goods sold (COGS).
The COGS formula is Manufacturing Price x Quantity = COGS.
Is beginning inventory a current asset?
Yes, beginning inventory is considered a current asset. Current assets are accounts that track what a company owns and uses in a year, which makes beginning inventory a current asset.