Table of Contents
** Minutes
Why is ending inventory important?
How to calculate ending inventory using the ending inventory formula
Ending inventory methods and examples
What would you like to learn?
When it comes to inventory accounting, knowing your ending inventory is essential. But calculating how much sellable inventory you have on hand at the end of an accounting period can be a challenge. That’s why it’s important to understand how to best calculate the value of your ending inventory and to choose the right inventory valuation method for your business.
In this article, you’ll learn why ending inventory is an important factor in calculating cost of goods sold, and how the right inventory management software can help you determine the value of your ending inventory at the end of the accounting period.
What is ending inventory?
Ending inventory refers to the sellable inventory you have left over at the end of an accounting period. When a given accounting period ends, you take your beginning inventory, add net purchases, and subtract the cost of goods sold (COGS) to find your ending inventory’s value. For a balance sheet to be complete, you’ll need to claim all inventory as an asset. Knowing your ending inventory value will impact your balance sheets and your taxes, so it’s important to calculate the value of your inventory correctly.
Ending inventory vs. closing inventory
Another name for ending inventory is closing inventory. The two terms are synonymous, as both refer to the amount of sellable inventory available at the point when a particular accounting period ends, or “closes”.
Why is ending inventory important?
You’ll always want to know much you’re selling — and how much you’re not selling! Ecommerce inventory can be seen as just another cost until it gets sold. In ecommerce, calculating ending inventory is a business best practice as well as an important part of the accounting process.
How to calculate ending inventory using the ending inventory formula
The basic formula for calculating ending inventory is easy:
Beginning Inventory + Net Purchases – COGS = Ending Inventory
Your beginning inventory is the last period’s ending inventory. The net purchases are the items you’ve bought and added to your inventory count. The cost of goods sold includes the total cost of purchasing or manufacturing finished goods that are ready to sell.

The simplest way to calculate ending inventory is to do a physical inventory count. But most of the time it doesn’t make sense to do a physical count, especially if you have a large amount of inventory to keep track of.
[CP_CALCULATED_FIELDS id=7]
Fortunately there are better ways to calculate ending inventory that provides more accuracy and is more efficient. For instance, using a third-party logistics (3PL) provider like ShipBob and integrating their fulfillment technology with inventory management solution like Cin7 makes finding the value of ending inventory a breeze.
Ending inventory methods and examples
There are several different ways to calculate the value of your ending inventory. The method you choose will impact everything from budgeting to inventory reorder quantity, and most importantly — growth profit. The method used to determine the value of ending inventory will impact financial results, so be sure to choose a method that’s right for your business and stay consistent with it.
FIFO method (first in, first out)
FIFO is an accounting method that assumes the inventory you purchased most recently was sold first. Using this method, the cost of your most recent inventory purchases are added to your COGS before your earlier purchases, which are added to your ending inventory.
For example, let’s say you bought 5 of one SKU at $15 each and then another 5 of the same SKU at $20 each a few months later. If these 10 same products are in your available inventory and you sell 5 of them, using FIFO you would sell the first ones you bought at $15 each and record $70 as the cost of goods sold.

Accountants and business owners choose FIFO periods of high prices or inflation to produce a higher value of ending inventory than the alternative method, LIFO (last in, first out method).
LIFO method (last in, first out)
Using the LIFO method, the most recently purchased inventory items are the ones that are sold and shipped out first. Simply put: goods that are purchases later are sold earlier.
For example, let’s use the same example as above of purchasing 5 of one SKU at $15 each and then another 5 of the same SKU at $20 each. If you sell 5 units using the LIFO technique, you would sell the 5 items you purchased most recently at $20 each and record $100 as the cost of goods sold.
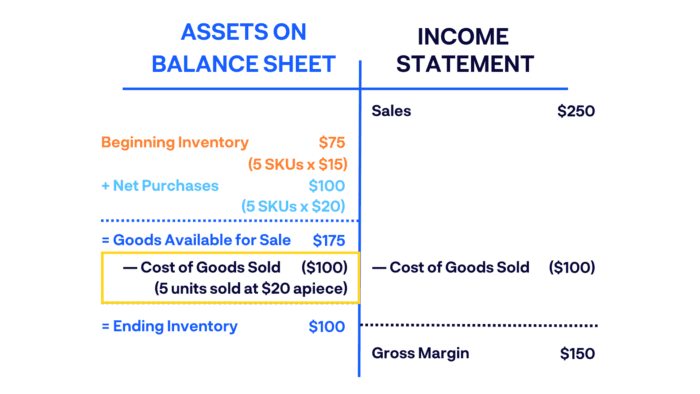
Accountants might suggest using LIFO during times of decreasing prices.
Weighted average method
Weighted average method (WAC) is determined by dividing the total amount you spent on the inventory you have on hand by the total number of items on hand. This provides an averages of the cost of purchased goods in your ending inventory.
For example, during the fiscal year you started with a beginning inventory balance of 100 items at $2.50 each. You purchased an additional 300 items at $3.50 each later on. Your ending inventory would include 400 items valued at $3.25 each, with a total value of $1,300 (assuming no purchases were made during this time).
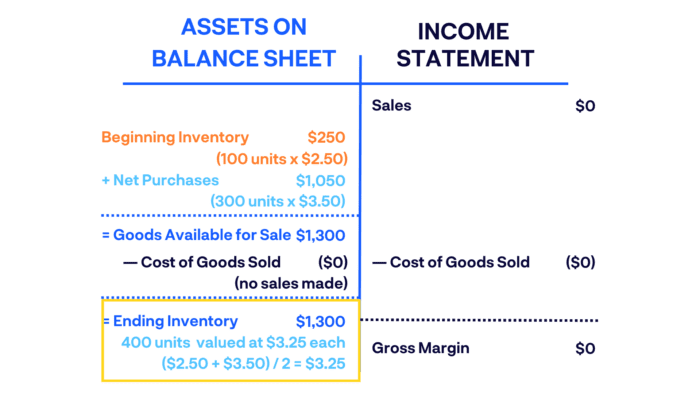
WAC is the simplest way to value ending inventory, and it makes the most sense to use when all products sold are identical.
How to use ending inventory
Once you’ve calculated your business’s ending inventory, you can use that information in many ways. Here are just some of the things brands can do after they’ve calculated ending inventory for a given period.
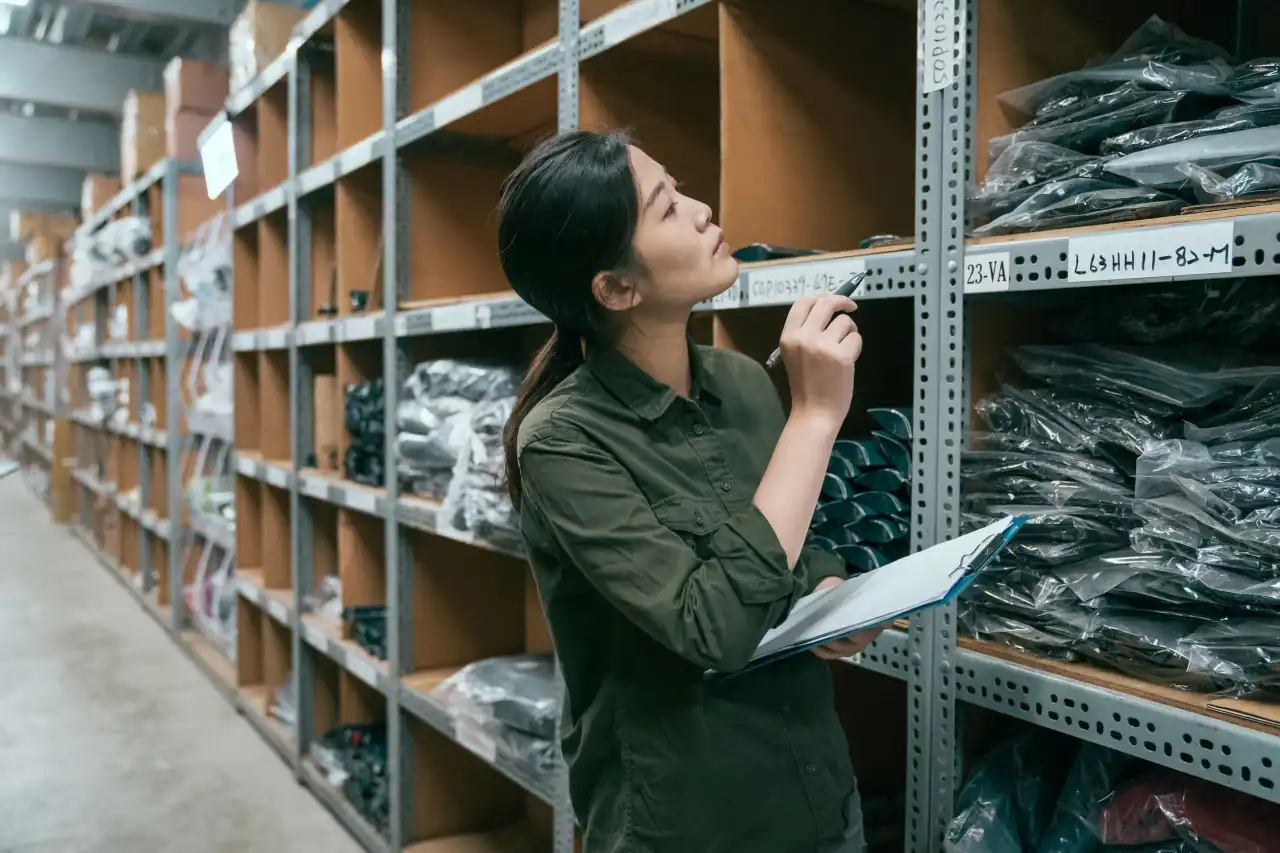
Match inventory recorded with actual inventory
You want to make sure that the figures on your inventory balance sheet match up with what’s currently in your warehouse. Knowing your ending inventory verifies the inventory that you have recorded matches the actual physical inventory you have on hand. If your inventory levels are less than they should be, this could be a sign of inventory shrinkage due to accounting error, theft, or a variety of other issues.

Calculate the net income
Likewise, you want to know the exact income statement i.e how much revenue you’re making on what you’re selling. Once you calculate ending inventory, you’ll have a clear understanding of whether your actual inventory matches the recorded inventory. If the numbers don’t match up, this could be a sign that you’re paying too much for the initial purchase of goods based on current market value, or that it’s time to rethink your pricing strategy.
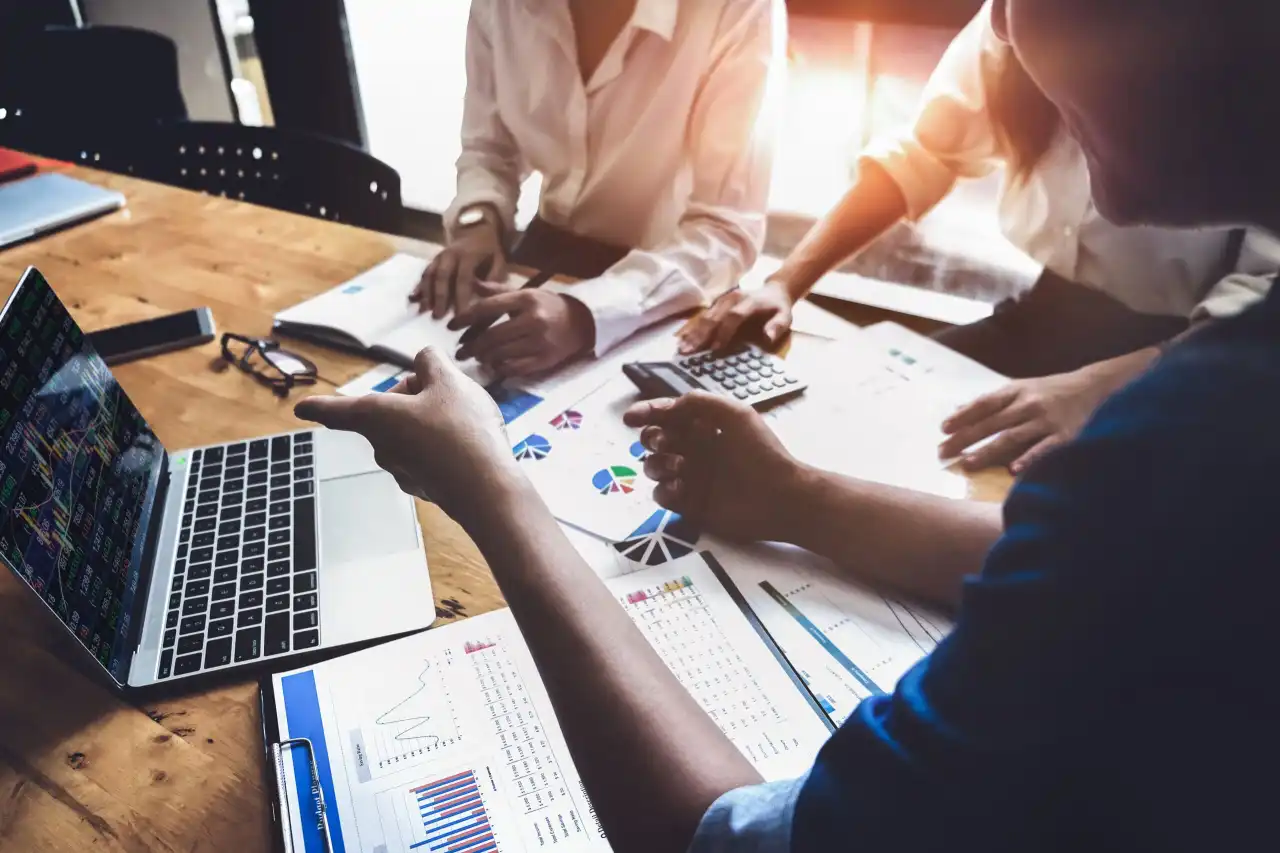
Ensures accuracy for future reports
Remember how ending inventory is calculated from beginning inventory? It goes the other way too. A given accounting period’s beginning inventory is calculated from the previous period’s ending inventory. Beginning balance is calculated from the previous reporting period’s ending balance. Therefore it’s crucial that the correct ending inventory is calculated correctly in your balance sheet.
There are several ways to calculate ending inventory, so it’s best to stick with one method every year to avoid discrepancies in future reports.
How 3PLs help improve ending inventory management
Partnering with a 3PL like ShipBob and integrating their technology with Cin7 can make the process of tracking inventory much easier and simpler. Here’s how.
1. Accurate inventory tracking with ShipBob + Cin7
ShipBob is a tech-enabled 3PL. ShipBob’ built-in inventory management tools can be directly integrated with Cin7, the market leader in inventory management software. That way, you can track inventory from one dashboard, helping you make more accurate buying and selling decisions, provide better customer service, and save on inventory and logistics costs.
Inventory tracking tasks that are normally time-consuming (like calculating or valuing ending inventory) can be done in a snap — or just a few clicks. Unlike other inventory solutions, Cin7 tracks actual inventory costs, not average costs, for more accurate COGS.
With ShipBob as your 3PL and Cin7 as your inventory management solution, you have the option to split inventory across multiple fulfillment centers while tracking inventory levels all in one place.
2. Custom reports and forecasting
With ShipBob, you can easily sync order fulfillment with an inventory management solution like Cin7 to help optimize your supply chain and centralize inventory reporting. With ShipBob’s analytics and reporting tool, you can easily track inventory days on hand and other metrics like:
- Historical stock levels at any point in time in any location
- Days left until a SKU will be out of stock
- Sales frequency across channels
- Product demand compared to previous periods
- Best-selling and slowest-moving items
- And much more
Cin7 also aggregates this information, and combined with data from its accounting and 550+ other app integrations, it offers an unbeatable analytics and reporting package for any product business looking to optimize inventory across all locations and sales channels.
Get in touch with ShipBob today to learn how our fulfillment services and technology can help your ecommerce business, and talk to the inventory experts at Cin7 to find out how inventory management software can simplify your business, even as you open up new sales channels.
Ending inventory FAQ
Here are some of the most common questions ecommerce businesses have when it comes to calculating ending inventory.
What is included in ending inventory?
The basic formula for calculating ending inventory is: Beginning inventory + net purchases – COGS = ending inventory. Your beginning inventory is the last period’s ending inventory. The net purchases are the items you’ve bought and added to your inventory count. The cost of goods sold includes the total cost of purchasing inventory.
What is included in ending inventory?
Ending inventory includes the final value of the inventory you have on hand at the end of an accounting period, after the total purchase of inventory and items sold within that time period are calculated.
How do you find ending inventory using FIFO?
FIFO stands for “First In, First Out.” It is an accounting method that assumes the inventory you purchased most recently was sold first. Using this method, the cost of your most recent inventory purchases are added to your COGS before your earlier purchases, which are added to your ending inventory.
What is the ending balance in finished goods?
Finished goods refers to the product you sell, not the component you purchase to make an item. The ending balance in finished goods is the total value of sellable inventory you have on hand at the end of an accounting period.
What is ending inventory on a balance sheet?
At the close of each accounting period, ending inventory is recorded as a current asset on a business’s balance sheet. Because it is inventory that is viable to be sold, it belongs on the “asset” side of the balance sheet, rather than liabilities.