Globalization impacts so much of our day-to-day lives – and your ecommerce supply chain is no exception.
It has never been easier to partner with foreign businesses, manufacture in other countries, and sell internationally, and more and more businesses are taking advantage of the benefits that come from taking a global approach to logistics.
This approach has become so popular that, even if you operate entirely domestically, your business will probably still be impacted by the global supply chain – especially if disasters, policy changes, or world events make cross-border collaboration difficult.
This means that no matter how you run your business, it’s important to understand how global supply chains work. In this article, we’ll dive deep into the key components of global supply chains, the challenges they pose, and how expert supply chain partners like ShipBob can help you build a reliable and efficient one.
Understanding global supply chains
A global supply chain refers to a network of businesses, parties, and stakeholders across multiple countries that are all involved in producing, transporting, and selling goods for an ecommerce company.
For example, if you source raw materials from China, manufacture the products in Vietnam, and sell it in the United States, you have a global supply chain. Even if you import finished goods directly from Australia and sell them in Canada, that also qualifies as a global supply chain.
This type of ecommerce supply chain allows businesses to tap into more economical resources such as labor, materials, and services to reduce their operational costs.
Key components of global supply chains
Global supply chains are extremely complex and are comprised of many different stages and functions. Here are some of the basic building blocks that make up a global supply chain.
Sourcing and diversification
Many businesses look to overseas suppliers and manufacturers to source their inventory. This is often because it allows brands to tap into cheaper labor sources and materials, and because it may give brands access to products or raw materials that aren’t available anywhere else.
Additionally, using a global supply chain allows you to diversify product sourcing. That way, instead of relying on just one supplier in a single country, you can source your products from multiple countries, enabling you to stay stocked even in case of disruptions.
Logistics planning
Sourcing and distributing goods across borders and international waters tends to complicate your logistics. You have to strategically plan how, when, and where you source and transport your products to ensure that you are turning a profit and that everything gets where it needs to go on time and in full.
Logistics planning in a global supply chain involves planning how goods should be transported and distributed across different regions and countries. Through proper logistics planning, you brand can:
- Minimize shipping costs
- Speed up transit times
- Avoid stockouts and backorders
- Reduce operations costs
- Stay in compliance with international laws and regulations
“Logistics is something you never think about until it stops working, and we’ve never come to that point with ShipBob. Everything just works. We are super happy with ShipBob and very impressed by how well they’ve pumped out our large volume of orders.”
Sergio Tache, CEO of Dossier
Risk management
With factors like international politics, global trade laws and regulations, unexpected crises, and the global economy impacting international ecommerce, the global supply is vulnerable to changes and disruptions. As such, risk management is a vital element in global supply chain management.
It’s important to prepare solutions and contingency plans to address these vulnerabilities and improve supply chain agility and supply chain resilience, so you can ensure that your global operations aren’t heavily impacted by changes or issues in global markets.
Production
Many countries offer brands lower production costs (often as a result of a lower cost of living and less expensive labor) to ecommerce brands. As a result, retailers will often manufacture or produce their goods in other countries through foreign production partners in order to minimize costs and increase their bottom line.
Transportation
Transportation is an absolutely essential element of global supply chains, as without international transportation methods, brands would not be able to move goods between geographies.
As the raw materials, parts, or finished goods get transported across different regions and countries, you’ll want to make sure that you’re using the most suitable transportation methods to keep costs low and your operations efficient.
You will also need to research, achieve, and maintain compliance with international regulations pertaining to how, when, and in what amounts you transport goods (as different countries will have their own rules about importing and exporting products and materials).
Distribution
Many global supply chains involve a distribution network consisting of several stakeholders, such as retailers, wholesalers, distributors, and ecommerce stores. Effective distribution management is necessary to ensure that goods seamlessly pass between these parties to ensure fast and affordable fulfillment while maintaining your bottom line.
Challenges facing international supply chains
As beneficial as global supply chains can be for businesses and consumers alike, they are not without their challenges. To avoid shortages, delays, and disruptions, it’s important to prepare for these challenges when building your own global value chain.
Supply chain visibility and complexity
When you work with international supply chain partners, you may experience challenges collecting up-to-date and accurate data across multiple sources. Siloed departments and outdated or out-of-sync supply chain technology prevent businesses from accessing real-time data, which inhibits your supply chain visibility and prevents you from taking timely action and making timely decisions.
Geopolitical tensions and trade policies
Your partnerships with global supply chain players could easily be affected by changes in local and international trade policies. Similarly, political tensions happening in one country could quickly snowball into larger problems that lead to supply chain disruptions.
For example, the Russo-Ukrainian war has disrupted several aspects of international trade, leading to global supply chain issues. It has led to manufacturers suspending their operations in Russia, while price hikes affected the cost of raw materials and transportation in certain markets.
Global health pandemics
Pandemics are another major challenge that have the potential to devastate global supply chains. For instance, the COVID-19 pandemic resulted in businesses having to suspend their operations while international transport stalled for months on end. It eventually led to supply chain bottlenecks as suppliers struggled to send goods to overseas businesses, resulting in inventory stockouts and shortages on a global scale. Moreover, lockdowns and health concerns prevented many businesses from resuming their operations, which further impacted their bottom line.
Cybersecurity threats
You often don’t have control over the cybersecurity measures that your international supply chain partners have in place. Unfortunately, a partner’s outdated technology or insufficient preventative measures could easily become a security risk that affects your business. You could stand to lose valuable data or expose sensitive information to malicious scammers and hackers, resulting in huge losses – not to mention the loss of trust with your customers.
Environmental concerns and sustainability
With rising concerns over climate change, many brands intentionally incorporate sustainable practices into their global supply chains to minimize their environmental impact. However, a sustainable supply chain may increase your costs and require a complete overhaul of existing practices, especially if you implement eco-friendly practices on a global scale.
Logistics and transportation volatility
When it comes to international supply chains, logistics and transport operations are prone to disruptions resulting from issues such as road blockages, port congestion, natural disasters, and more. A problem that disrupts transportation in one country could eventually lead to bottlenecks further down the line.
How ShipBob powers global supply chains
With global supply chains being so complex, it’s no wonder that lots of ecommerce brands choose to partner with supply chain experts like ShipBob to manage their port-to-porch operations. ShipBob’s suite of services provides scaling brands the capabilities they need to streamline their global supply chains, save money, and improve efficiency in everything from freight shipping to fulfillment.
Here are just some of the solutions that ShipBob customers leverage to optimize their global supply chain management.
End-to-end freight management
Brands can ship freight to ShipBob’s global fulfillment network using FreightBob, an end-to-end managed freight and inventory distribution program that enables merchants to pick from a variety of preferred freight providers, optimize freight costs, and get access to sailings from most global locations directly to ShipBob’s receiving hubs and fulfillment centers.
ShipBob also simplifies inbound and outbound freight shipments to or from our fulfillment centers through a program called ShipBob Freight. Merchants who use ShipBob Freight can save on freight costs, time spent on transit and coordination, with all appointments booked for them, and simplify vendor management through ShipBob’s all-in-one logistics solution.
“We had 900 backorders and needed to get our inventory over from Asia ASAP. We, of course, needed our backorders shipped out to our customers who were waiting, immediately.
With FreightBob, we were able to ship from Shanghai through the LA / Long Beach port. We then were able to send out to our customers in less than 3 weeks. To watch ShipBob ship out 900 orders for us in a day, then complete another fulfillment of 2,000 orders in a single day the next week, it was magical. They made it look so easy. And with FreightBob, it’s too easy to use to not utilize.
Time is money. The more time that I can save spending energy on things like freight and fulfillment, the more time I can spend on other details for my company. To know that I can trust somebody to complete the tedious stuff and be organized like I would; what a stress reliever.”
Emily Coolbaugh, Logistics Coordinator at Driveline Baseball
Advanced inventory management systems
ShipBob’s software features built-in inventory management capabilities, including real-time visibility into your inventory levels across channels and locations. With this data, you’ll always know exactly how much inventory you have on hand, enabling you to time replenishment from foreign suppliers and manufacturers correctly to avoid stockouts and backorders.

You can also track and analyze past order and inventory data to improve demand forecasting and adjust your procurement strategy to meet customer demand. Plus, ShipBob’s analytics dashboard displays key metrics that give you insight into your global supply chain performance, including:
- Average order lead time and transit time
- Inventory turnover
- Average shipping cost
- Storage cost
“I can’t say enough about ShipBob’s software and reporting capabilities. It really has made things easy for us to look at the data and make better decisions. Not all partners are set up that way – oftentimes when you’re using other providers’ technology, you have to pull the data yourself, and there’s a lot of work to be done on the back end.”
Ryan Steffenson, Senior Manager, Channel Operations at Tonies
Strategic warehouse locations
With our dozens of global fulfillment centers, ShipBob lets you store your inventory across multiple warehouses in various countries and regions. This means you can store your inventory closer to your customers and ship them out from the fulfillment center closest to the orders’ end destination, speeding up deliveries while reducing transportation costs.
ShipBob’s network spans 3 continents and includes 50+ fulfillment centers (all powered by ShipBob’s proprietary warehouse management technology) for brands to leverage, with locations across the US and in Europe, Canada, Australia, and the United Kingdom. Using this global footprint, brands can effectively scale their operations and better serve international customers without investing capital, time, and effort into building their own facility.
ShipBob’s dashboard even offers an analytics tool to help brands determine the most strategic split of inventory across multiple ShipBob locations. This tool uses your business’s real order data to calculate the inventory allocation plan that will result in the lowest average fulfillment cost and transit time – and through ShipBob’s Inventory Placement Program, you can send all your inventory to a single ShipBob receiving hub and we’ll take care of distributing stock regionally for you.
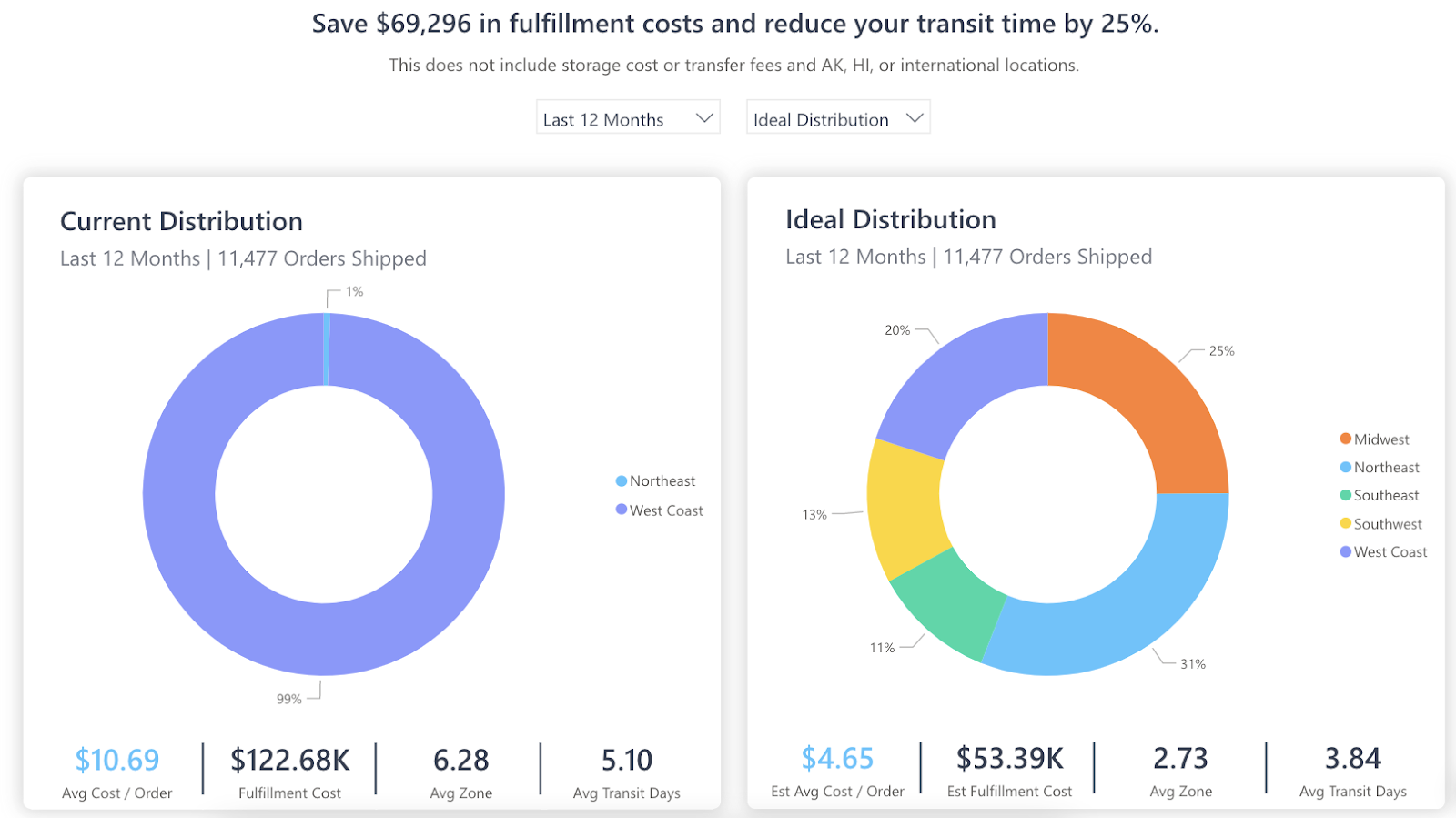
“Trying to figure out how much of what inventory to send where could be wildly complex for our supply chain managers – but since ShipBob automatically tracks our order and shipping data for us, that data basically tells us our optimal inventory distribution. We also get automatic reminders notifying us well before inventory levels are getting depleted, so we don’t have to constantly be checking our stock levels. IPP has saved our supply chain team a lot of extra work, and they also feel really supported by ShipBob and know that they can turn to them for help.”
Tyler McCann, Co-Founder of Taste Salud
Scalable, omnichannel fulfillment solutions
Whether you’re just getting started or climbing to $100M in revenue, ShipBob can flex to handle surges in your order volume while delivering the capabilities you need to scale, when you need them. As you scale, your business can leverage growth levers like:
- B2B fulfillment, including EDI-compliant retail dropshipping and distribution
- Integrations with dozens of major retailers, ecommerce platforms, marketplaces, and tools to fit seamlessly in your existing tech stack
- Customization features like gift notes, marketing inserts, and branded packaging to curate an unforgettable unboxing experience
- DDP shipping for international orders to eliminate surprises for customers and simplify cross-border purchases
- 2-day shipping options to meet and beat customers’ expectations for fast, affordable delivery and build loyalty
- ShipBob’s warehouse management system (WMS), which you can use to optimize your own warehouse’s operational efficiency and order accuracy
Exceptional customer support
ShipBob customers enjoy 24/7 support with proactive communication that allows them to resolve issues quickly and keep your operations running smoothly. Moreover, a dedicated account manager guides you through the setup process while providing valuable guidance to improve your warehouse layout and operational efficiency.
“I’m a big believer in raving about really good quality service – especially when it comes to customer support. At Elle Sera, we hold ourselves to an extremely high standard for customer support, and we expect the same from our partners. The same can be said of everyone on the ShipBob team, down to the people picking and packing orders in the fulfillment center.
I remember a while ago, I got a call from one of ShipBob’s fulfillment center associates telling me that for some reason, a fulfillment rule in the system had not been turned on. I was about to panic, but she immediately said to me, ‘I knew you wouldn’t want to worry about work this weekend, so I’ve taken the liberty of fixing the problem for you.’
It’s things like that, that set ShipBob’s support apart on another level. To not only pinpoint the issue right away but understand the impact it would have on me personally, and take the initiative to fix it, no questions asked – that proactivity is what makes ShipBob a truly fantastic partner and helps me trust that they have everything under control.”
Kelly Bond, Operations Manager at Elle Sera
For more information about how ShipBob can help you manage your global supply chain, click the button below.
Global supply chains FAQs
Below are answers to the most commonly asked questions about global supply chains.
What makes a supply chain global?
A supply chain is global when two or more of its stakeholders, vendors, or parties operate in different countries.
How do global supply chains manage regulatory compliance?
Global supply chains can manage regulatory compliance through careful research into each involved country’s unique laws, regulations, and certification requirements regarding ecommerce and supply chains. Brands may need to adjust their policies and procedures to maintain compliance.
How does ShipBob enhance supply chain resilience?
ShipBob enhances supply chain resilience with real-time visibility that allows for timely and informed decision making. This data informs your inventory needs, helps ensures that you’re stocking up on time, and enables you to plan ahead to prevent disruptions.
Moreover, ShipBob’s global fulfillment network allows merchants to strategically store their inventory across various locations so they have stock reserves in case of inventory loss or damage, and can still fulfill orders despite any disruptions.
How do global supply chain disruptions affect consumer prices?
Global supply chain disruptions tend to make raw materials, production, transportation, and distribution more expensive. This increases inventory costs for ecommerce brands, which may raise consumer prices to offset the extra costs and preserve their bottom line.