Table of Contents
** Minutes
Understanding ecommerce warehouse congestion
Strategies for managing warehouse congestion
Think of how hard it is to move in a crowded space. Now imagine trying to stow inventory, pick products, and pack orders in a crowded warehouse – it’s a recipe for disaster.
While ecommerce businesses want to make sure that their warehouse is well-stocked, clutter and crowding in your warehouse space – also known as warehouse congestion – can lead to inefficiencies, safety hazards, and fulfillment errors.
To keep your workers safe and your operations streamlined, it’s important to avoid warehouse congestion.
In this article, we’ll take a closer look at what causes warehouse congestion, how it affects brands, and how to manage your warehouse and inventory planning to minimize it.
Understanding ecommerce warehouse congestion
Warehouse congestion refers to overcrowding, clutter, or traffic within a warehousing space that obstructs movement and slows down regular warehousing activities.
When a warehouse is hard to move around or navigate through, it’s harder for workers to perform tasks. This can:
- Halt or stall the flow of inventory
- Confuse and frustrate workers
- Create safety hazards
- Hinder a brand’s ability to fulfill customer orders in a timely manner
Common causes of warehouse congestion
Many factors can contribute to warehouse congestion. Here are some of the most common root causes of warehouse congestion for ecommerce brands.
Insufficient storage space
The easiest explanation for warehouse congestion is having a lot of inventory, and no place to put it. Whether your warehouse is too small to store the amount of stock you need to meet demand, or whether you just ordered too much stock, exceeding storage capacity usually results in warehouse congestion.
Poor layout design
Warehouse congestion can also be a result of a warehouse layout that restricts movement or creates inefficiencies.
For example, if your warehouse’s floorplan doesn’t leave enough space in each aisle for a forklift or other equipment to pass through, workers will have to spend time and effort finding a different way to perform the necessary tasks. This slows down your operation and reduces efficiency.
Inefficient processes and technology
Standard operating procedures can also cause warehouse congestion. For instance, if a brand instructs pickers to pick one order at a time and drop off each individual order at a packing station before beginning another, they will not be able to pick many orders in a given time period. In this case, the picking strategy is holding pickers back from efficiency and producing congestion.
Outdated, cumbersome technology only multiplies inefficiencies. Congestion is common when a brand uses on smart warehousing technology that is:
- Unreliable (frequently glitching or broken)
- Not easy to navigate or use
- Difficult to train workers on
- Obsolete
The impact on businesses
Warehouse congestion isn’t just annoying – it’s actively harmful for businesses. Here are some of the most common ways that warehouse congestion impacts ecommerce operations.
Delayed shipments
In a congested warehouse, workers can’t perform their tasks efficiently, meaning they may not be able to pick and pack orders quickly enough to get orders to customers on time. As a result, shipments get delayed, and customers get disgruntled.
Customer dissatisfaction
With orders taking longer to reach your customers, warehouse congestion can seriously impact customer satisfaction. Fulfillment errors and inventory damage are also common when warehousing space are overcrowded – both of which further upset customers and discourage them from purchasing again.
Increased costs
Since workers are unable to move efficiently in a congested warehouse, they take longer to complete their assigned tasks. This adds to increased labor costs and overhead expenses, which affect your bottom line.
It is also harder to count, audit, and manage one’s inventory in a cluttered warehouse, which may result in inaccurate data on inventory levels. This can lead you to accidentally over- or under-stock certain SKUs, producing costly stockouts and backorders.
Strategies for managing warehouse congestion
Now that we’ve covered some of the reasons why warehouse congestion happens and what it does, let’s dive deeper into how you can keep your own warehouse’s congestion in check. Here are a few tips for minimizing warehouse congestion, plus examples of these strategies in action.
Optimize layout and design
Warehousing efficiency starts with your warehouse setup. Consider your internal workflows, and select a configuration of storage and workstations that will minimize travel distances, create definite pathways, and allow seamless movement for workers and vehicles.
When arranging your inventory storage, make sure you employ a warehouse slotting strategy that makes sense for your business. You could group products by size, weight, or other shared characteristics. Alternatively, dynamic slotting techniques are ideal for warehouses that deal in huge volumes of transient, high-demand products.
You should also incorporate inventory storage solutions and racking systems that allow you to maximize space utilization. Besides using appropriate pallet racks and shelving units, look for advanced storage systems that are ideal for your warehouse. Vertical carousel modules, for instance, help you make the most of vertical space in your warehouse.
Implement efficient processes
Sometimes, you can clean up warehouse congestion simply by streamlining your daily processes and running a leaner supply chain. This can include:
- Eliminating unnecessary activities.
- Tracking inventory over time to avoid accumulating deadstock and inventory obsoletion.
- Leveraging more efficient picking strategies, such as batch and zone picking, to minimize workflow bottlenecks.
- Conducting regular warehouse audits to measure efficiency and waste.
- Training staff on the safest and most time-effective ways to perform tasks.
Leverage technology
The right warehouse technologies make it much easier for brands of all sizes to minimize warehouse congestion.
For starters, employing inventory management software enables you to both track inventory levels and dig into historical sales data. With these capabilities, your brand can accurately forecast demand so that you don’t overstock your warehouse.
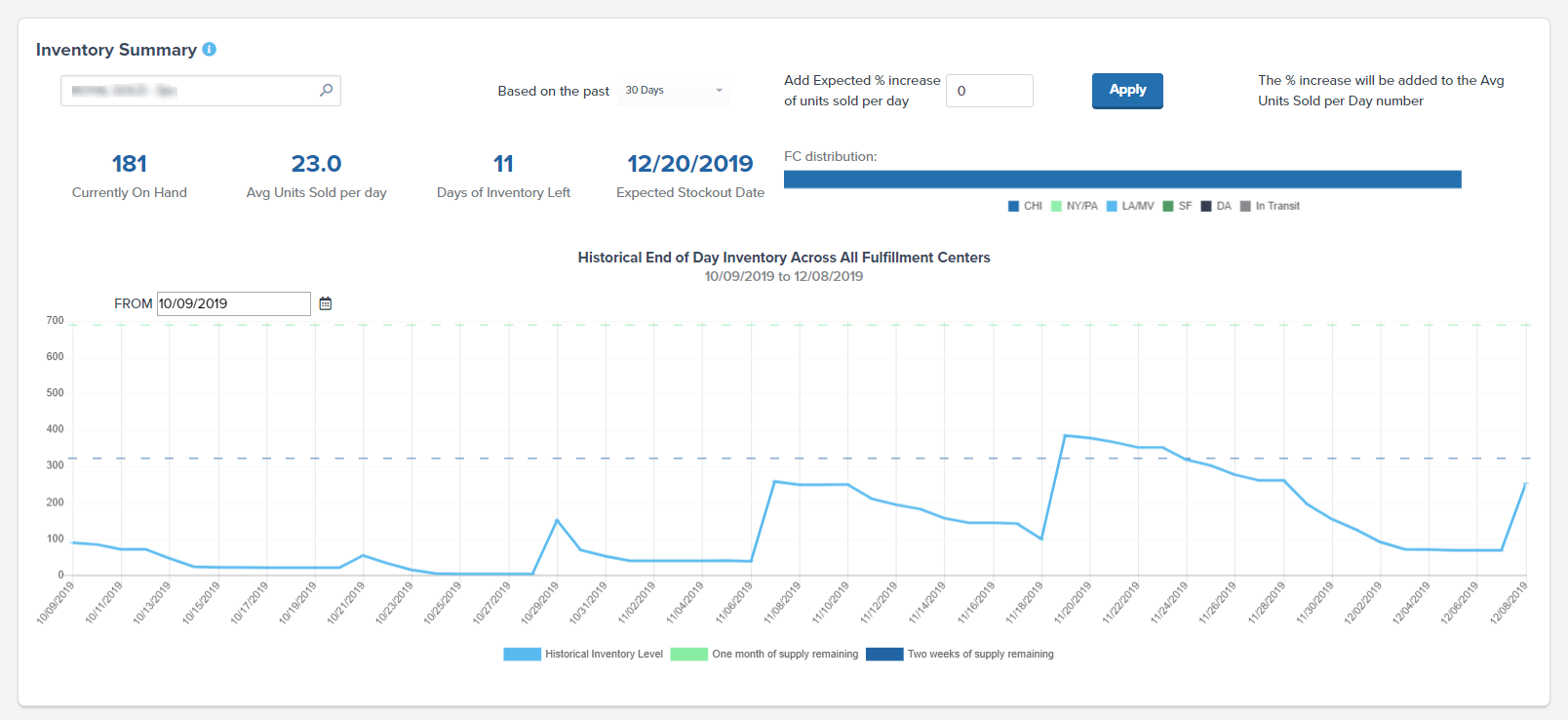
Technological equipment like RFID tags and barcode scanners go hand-in-hand with inventory management software. By scanning SKU barcodes and storage location tags during the picking and packing process, you can update stock counts in real-time and keep your inventory and storage organized.
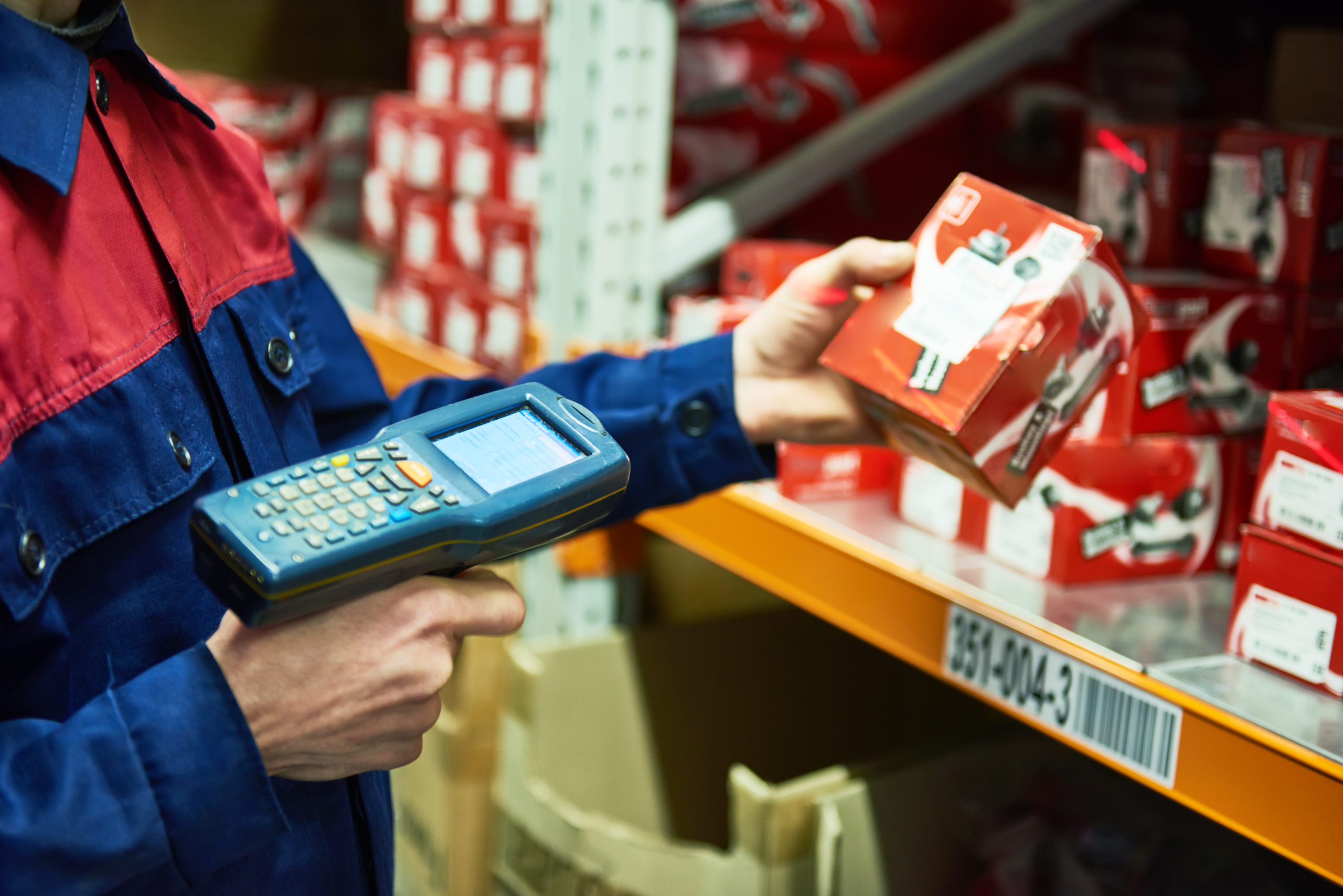

Warehouse management systems are also vital to reducing warehouse congestion. The right WMS enhances visibility and gives you better control over your warehouse activities. For instance, ShipBob’s WMS enables the brands who use it to power their warehouses to:
- Track staff productivity
- Achieve location-specific inventory visibility
- Access intelligent cycle counts and order fulfillment metrics across all warehouses
- Leverage flexible picking methods, including batch, auto-cluster, custom cluster, and single-order picking
- Reduce packing errors with prescriptive, visual step-by-step packing flows and built-in visuals
- Integrate with major ecommerce platforms and tools to streamline omnichannel fulfillment
With these insights and capabilities, you can anticipate potential inefficiencies and correct them before they turn into full-blown congestion.
Check out ShipBob's Warehouse Management System (WMS)
ShipBob's WMS helps your warehouse reduce picking errors, manage inventory in real time, and fulfill orders faster.
Case study: ShipBob’s approach to warehouse congestion
Merchants can use ShipBob’s WMS – the same WMS that powers ShipBob’s dozens of fulfillment centers around the world – in their own warehouses to reduce congestion and improve warehouse efficiency.
Here’s how the viral netball game brand Spikeball leveraged ShipBob’s WMS to do just that.
The challenge
Before partnering with ShipBob, Spikeball relied on a home-grown approach to warehouse management – but it was causing compounding inefficiencies and operational congestion.
The brand used label-generation software in their warehouse. They had to print labels order by order, trusting the manager’s experience to determine what a certain order would weigh and what type of box it would need. If they got it wrong, they would inevitably get a bill from the carrier.
Their warehouse also didn’t have pick locations or a computer at the packing table, and had a team of 3-4 people spending all day packing orders just to keep up with their order volume.
Spikeball knew it was time for a change – and since they were already leveraging one of ShipBob’s European fulfillment centers, they decided to give ShipBob’s WMS a try in their own warehouse.
The solution
With the help of a ShipBob Implementation Specialist, Spikeball began reworking their warehouse processes.
ShipBob’s WMS and support team first helped them create more efficient pick paths:
“Prior to ShipBob, we had our most popular products at the front. Through the implementation process we learned that if you’re commonly picking certain items, they should be stored in the back so you aren’t carrying them around while you’re picking other items. Our best sellers are at the end of the pick path now, so once we’ve picked those, we’re already back at the pack stations.”
Adam LaGesse, Global Warehousing Director at Spikeball.
They also changed the way they stowed products to make the picking process more intuitive and improve order accuracy:
“We used to have similar items in the same area — take shirts, for instance. Because they were so close together, there was a high likelihood that we picked the wrong size or the wrong color because all of our shirts looked similar and were physically right beside each other. Once we set up ShipBob’s system, we were putting those similar items (that weren’t ordered together) in all different places in the warehouse. After that, our pick accuracy went way up.”
Adam LaGesse, Global Warehousing Director at Spikeball.
Finally, Spikeball used ShipBob’s WMS to automate fulfillment operations. They were able to stop relying on workers’ experiential knowledge and simplify the process:
“Now the process for picking and packing with ShipBob is very straightforward. All our manager has to do is pick the orders, bring them back to the pack station, pack them up, and send them out. Boom, done. Now she doesn’t have to worry about selecting carriers and putting weights and dimensions in herself, because the ShipBob WMS does that for her.”
Adam LaGesse, Global Warehousing Director at Spikeball
The results
Leveraging ShipBob’s WMS, Spikeball was able to streamline their warehousing operations. They finally have an automated system that makes fulfillment less stressful, and it’s enabled them to improve picking efficiency by 80% and achieve $400,000 in cost-savings on postage.
Conclusion
Warehouse congestion is a serious challenge that prevents ecommerce businesses from fulfilling orders efficiently and maximizing profitability.
The good news? Partnering with a warehousing and fulfillment provider like ShipBob can help you optimize your operations to reduce congestion – or even prevent it altogether.
Brands can outsource inventory storage, fulfillment, and shipping to ShipBob to take daily warehousing activities off their plate, and have an expert keep operations running smoothly. Or, if you’d prefer to keep operations in-house, ShipBob lets merchants use our WMS to optimize warehousing, access key data and insights, and achieve visibility. That way, you can stay in control of your warehouse while keeping congestion in check.
For more information on how ShipBob can help your brand improve its warehousing strategy, click the button below.
Warehouse congestion FAQs
Below are answers to common questions about warehouse congestion.
What causes warehouse congestion?
Too much physical inventory and not enough storage space, inefficient processes, and poor layout design are some of the main causes of warehouse congestion.
How does ShipBob help businesses manage warehouse congestion?
You can outsource warehousing and logistics functions like inventory storage, fulfillment, and shipping to ShipBob to optimize operational efficiency while avoiding warehouse congestion.
Alternatively, brands can use ShipBob’s warehouse management system (WMS) to reduce warehouse congestion in your own warehouse through best practices and leading inventory order, and fulfillment software.
Is warehouse congestion inevitable?
Most warehouses will experience some level of congestion, particularly during peak seasons. However, warehouse congestion is manageable with the right warehouse technologies and management strategies.