It’s tempting to think that it doesn’t matter how you run your warehouse, as long as customers get the right orders on time – but this couldn’t be farther from the truth.
What goes on inside your warehouse plays a vital role in the customer experience and the efficiency of your overall operations. It directly impacts the quality of goods being delivered, the speed of delivery, and the accuracy of customer orders – so it’s crucial for ecommerce businesses to maintain warehouse quality control to keep customers happy and their business running smoothly.
In this article, we’ll cover what warehouse quality control is, best practices for implementing quality control measures, and how warehousing and fulfillment experts like ShipBob can help you unlock better quality control.
What is warehouse quality control (and why is it important)?
Warehouse quality control refers to the rules, procedures, and strategies designed to ensure that goods are handled safely within a warehouse, and that orders are fulfilled correctly, in good condition, and in a timely manner.
Warehouse quality control measures may include checking inventory for damages, checking the condition of packages before they leave the warehouse, verifying if items are stored correctly, and more.
Following robust warehouse quality control processes helps you maintain specific quality standards in your ecommerce warehousing operations. It helps to minimize errors, improve accuracy, and reduce waste, all of which eventually translate to better operational efficiency, enhanced customer satisfaction, and improved cost savings.
Key components of warehouse quality control
Warehouse quality control a multifaceted endeavor, and businesses rely on many different procedures to monitor and maintain quality across warehousing activities. Some of the most important warehouse quality control measures include:
Product inspections
Goods are inspected at key stages to ensure that they’re undamaged and up to standard. This includes an incoming goods inspection, where the products arriving at the warehouse are checked for quantity, quality, and damage. Additionally, an outgoing goods quality check is also performed to ensure that the goods being shipped out are unbroken and (if products are perishable) not expired.
Accurate labeling
Having accurate labeling systems in place makes it easy for warehouse staff to identify where certain items are stored or should be stored. This streamlines the putaway and picking processes, ensuring better accuracy.
Proper storage
A crucial aspect of warehouse QC is ensuring that goods are stored in such a way that maintains their quality. This involves storing perishables at the right temperature and humidity, using appropriate protection for fragile items, keeping sensitive electronics away from areas with strong magnetic fields, and more. Warehouse setup and capacity should also be optimized to allow for easy movement and retrieval.
Inventory management
Businesses also rely on efficient inventory management strategies for better quality control in the warehouse. This allows them to maintain optimal stock levels and prevent issues related to overstocking, inventory obsoletion, and stockouts.
Order checks
Order checks are performed to ensure that the right items are shipped out in the right quantities. This ensures better order accuracy to meet customer expectations. It also minimizes the need for returns, saving significant time and money.
Regular warehouse audits
Conducting periodic warehouse audits to check for the effectiveness of their existing processes and the impact on overall quality enables you to identify opportunities for improvement, and keeping quality high.
What role do quality checks play in the warehouse?
You can’t have your eyes everywhere in your warehouse at once, but quality checks at key stages of your warehouse operations can drastically increase your order accuracy and overall quality. For instance:
- Receiving: Quality checks during the warehouse receiving process ensure that the products arriving at your warehouse are undamaged and in sellable condition.
- Putaway: During the putaway processes, quality checks ensure that items are stored at the right locations, making it easy for pickers to locate the correct items later on.
- Storage: Checking storage conditions (such as structural integrity of racks, temperatures, safety from leaks or hazards, etc.) helps to prevent damage and waste.
- Picking: Quality checks during warehouse picking ensure that your fulfillment staff picks the right items in the right quantities. Ideally, your team should use barcode scanners to locate the items and double-check they’re picking the right products needed for the order, and check any expiration dates on perishable products.
- Packing: Packers double-checking the items they’re packing against the customer’s order details ensures that they’re sending out the right items in the right quantities, improving order accuracy.
All these checks ultimately help prevent you from sending customers items that are in unsellable condition, from losing inventory to waste or damage, and from wasting time on inefficient processes.
Check out ShipBob's Warehouse Management System (WMS)
ShipBob's WMS helps your warehouse reduce picking errors, manage inventory in real time, and fulfill orders faster.
Implement these best practices to improve warehouse quality control
With so many aspects to warehousing, it can be hard to know how to improve quality control. Here are some best practices to implement to get started.

Establish quality checkpoints throughout the fulfillment process
The challenge with warehouse quality control is that there’s a risk of things going wrong at every stage of the warehouse workflow. Even if you’ve received high-quality products, they could easily get damaged from improper storage or handling, or get confused with a different product during picking. This makes it crucial to have multiple quality checkpoints in place throughout the fulfillment process.
With multiple checks and balances built into different warehousing activities, you have a higher chance of catching problems as they arise and resolving them before products get shipped out to your customers.

Training employees on quality control standards
Most quality issues are the result of human error – especially when employees don’t know knowing the quality standards they need to maintain or what problems to look for. Someone picking an item with defective packaging may not notice it and move the product through to packing if they’re unaware of what the packaging is supposed to look like. Alternatively, pickers may end up retrieving the wrong item if they fail to follow procedure and scan the product’s barcode to verify that they have the correct item.
This makes it crucial to train your warehouse staff on the quality control standards needed for your operation. Show them how to safely and correctly store and handle goods; train them on how to use tools and equipment to conduct a quality check within their respective processes; establish a standard of operations for each process, so team members know the exact protocol they need to follow for quality checks.
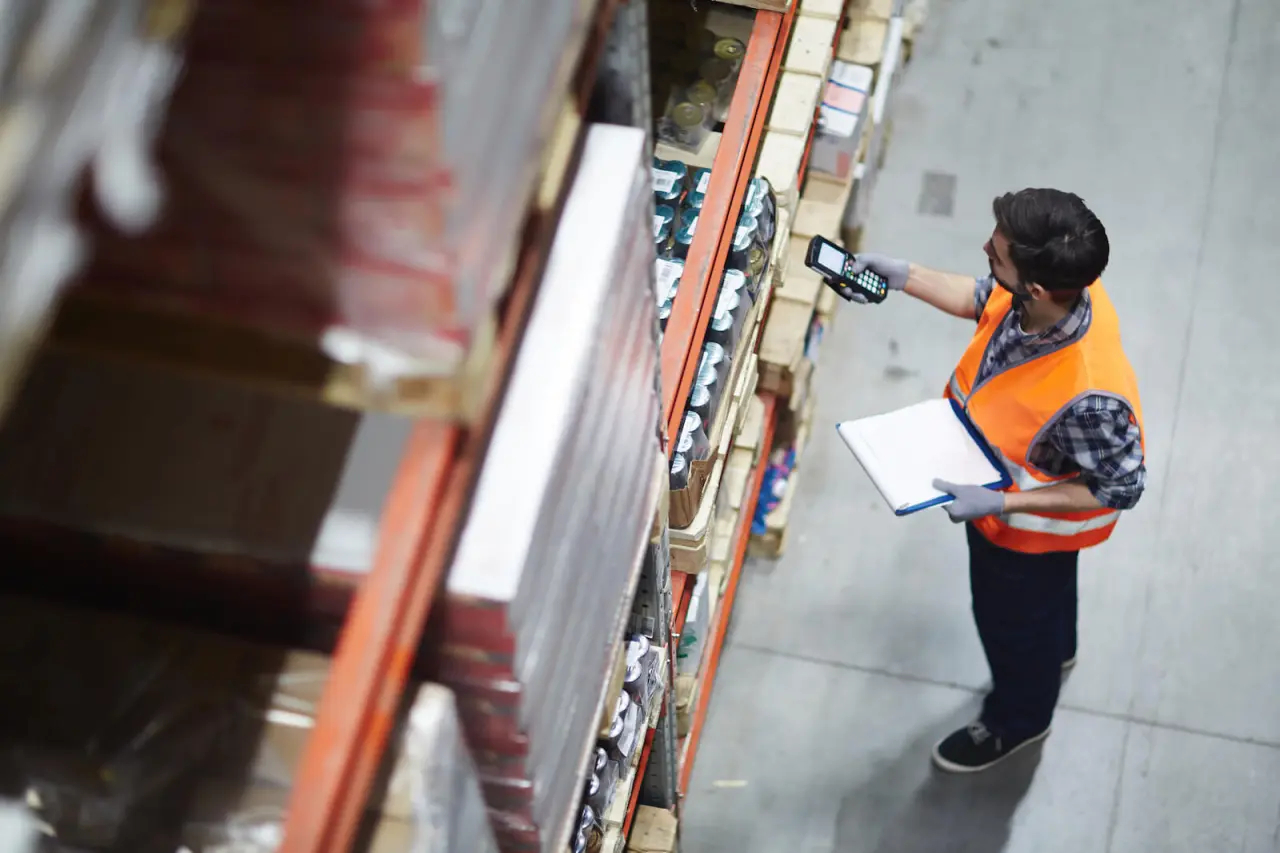
Adopt technology for quality control automation
Businesses can automate significant portions of their quality control processes with the right supply chain automation technology. This includes the use of warehouse management systems to monitor warehousing activities and easily detect deviations in key performance metrics.
You can also leverage AI-powered tools to generate optimized picking lists while IoT-enabled sensors can help you monitor warehouse temperatures and inventory levels in real time.
How fulfillment tech reinforces warehouse quality control
In modern warehouses, technology plays a huge role in quality control. With the right technology solutions powering fulfillment operations, you can simultaneously optimize fulfillment and boost order accuracy, speed, and quality – all with less manual effort on your team’s side.
Here are some of the most crucial technologies to implement in your warehouse for better warehouse quality control.
Ensure quality every time with a WMS
A warehouse management system (or WMS) lets you institute multiple checks and balances throughout your fulfillment process. The system serves as a single source of truth for your inventory, allowing fulfillment teams to easily verify products to reduces mis-picks and improves order accuracy.
For instance, ShipBob’s WMS includes:
- An intuitive dashboard gives visual step-by-step packing flows, reducing the risk of packing errors.
- Inventory data that is updated in real-time based on fulfillment activities and product movements to increase inventory accuracy.
- Recommendations for optimal pick methods and optimized picking routes to improve efficiency.
“ShipBob’s WMS makes it almost impossible to do things wrong. Eliminating the potential for human error during picking and packing has been great. That was our biggest problem before. Last time I checked, our error rate was less than 1%. We’re shipping out over 10,000 orders per month.“
Clint Sanders, VP of Operations of Bunker Branding
Real-time analytics for monitoring fulfillment accuracy
When it comes to quality control, real-time analytics dashboards enable businesses to monitor vital quality metrics. For instance, ShipBob provides real-time inventory and fulfillment insights to track inventory performance (such as which products are in the highest and lowest demand) and assess fulfillment performance.

You can use the analytics dashboard to get real-time insights on the number of orders fulfilled, shipped, and processing on a given day. This makes it easier to track if orders are being fulfilled as expected. You even get to see orders in “Exception” due to issues like insufficient stock or inactive/unknown SKUs, allowing you to fix the issue before it escalates.
“ShipBob’s reporting is very robust and meets all of our needs. We get visibility into receiving, order volume, SKU availability – everything from inbounds and inventory transactions to individual order statuses (whether it’s on hold, in processing, an exception order, and other detailed descriptions). All this data is real-time, meaning that we’re always seeing the most accurate, up-to-date information. Having this real-time data is crucial for my team, so the fact that there’s not hours of lag time waiting for data to update is huge.”
Ryan Steffenson, Senior Manager, Channel Operations at Tonies
Using IoT and automation for error reduction
Manual data entry and monitoring are prone to errors, which can lead to quality issues in the warehouse. Businesses can make use of IoT-enabled devices and automation tools to streamline many of their warehousing processes and ultimately enhance their quality control efforts.
For instance, barcode scanners can be used by warehouse staff to automatically capture and verify inventory data before storing or picking items. RFID tags can automatically track inventory movement and make it easier to monitor inventory levels. IoT sensors can help you monitor warehouse conditions and temperatures in real-time and automatically detect any discrepancies.
How ShipBob unlocks superior warehouse quality control
ShipBob’s sophisticated technology and world-leading fulfillment solutions empower businesses to maintain superior warehouse quality standards. With real-time visibility and custom fulfillment solutions, you can ensure that high-quality goods are consistently delivered on time to your customers.
Real-time tracking and automated error prevention
ShipBob’s powerful WMS and inventory tracking tools give you real-time insights into how goods are moving across your warehouse. This makes it easier to spot inconsistencies in inventory counts and orders, so you can fix problems quickly before they spiral out of control.
Warehouse staff can use also mobile scanners integrated with your WMS to verify inventory information and run multiple checks and balances throughout various aspects of your operations. This allows for efficient quality checks and significantly enhances order accuracy rates.
Custom packaging and kitting for reduced damage
Warehouse quality assurance is particularly challenging when you have to handle goods that need special care. ShipBob’s Customization Suite lets you take extra care of products according to their unique specifications.
Instead of a one-size-fits-all approach to packaging, you can take advantage of custom packaging and kitting services to ensure proper handling. Make use of packaging inserts and dunnage to give products extra protection and prevent damage in transit, or create ready-to-ship orders with all the products needed so items aren’t misplaced or lost in transit.
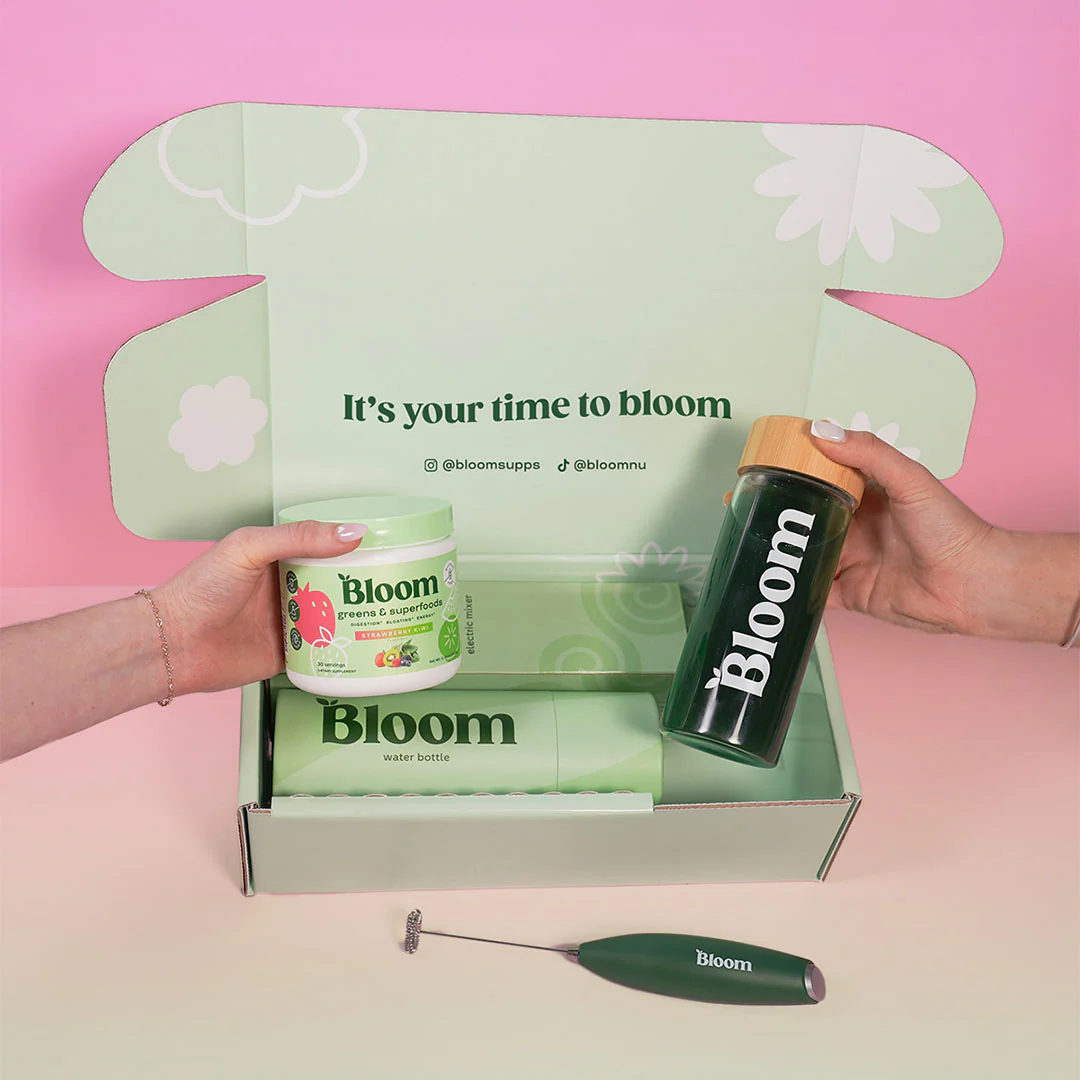

Inventory placement for accurate shipments
Merchants in the US can take advantage of ShipBob’s Inventory Placement Program to strategically distribute their inventory across different fulfillment centers. The program determines your ideal inventory distribution strategy across ShipBob’s fulfillment center network based on demand forecasting, historical sales data, and real-time sales trends. Simply send your inventory to one hub location, and the ShipBob team will handle the rest.
Once orders are placed on your website, they’re shipped out from the most optimal fulfillment center based on factors like proximity and stock availability. With a data-driven algorithm determining the entire process, there’s less room for error, allowing for more accurate shipments.
“When we first got started, we checked how ShipBob’s IPP was distributing our inventory based on the models we created when we did distribution in-house – they were on point. ShipBob’s machine learning data works. They took a container with 1,000 SKUs and knew exactly which inventory needed to go to which facilities. On top of time savings, we were able to realize cost savings because we didn’t have to make any inventory transfers. We send our inventory to ShipBob once, they receive it, and they distribute it across their US network. We’re saving thousands of dollars each month by using IPP. “
Cesar Contreras, Head of Supply Chain of Wholesome Goods
For more information on how ShipBob can help you improve warehouse quality control, click the button below to get in touch.
Warehouse quality control FAQs
Below are answers to the most commonly asked questions about warehouse quality control.
What are some common warehouse quality control challenges?
Some of the biggest challenges with warehouse quality control include lack of visibility, poor infrastructure, and lack of staff training.
How does ShipBob’s WMS help with quality control?
ShipBob’s WMS gives your warehouse team real-time visibility into warehousing activities and inventory movement, and includes multiple built-in checks and balances to streamline quality control.
What is SOP for quality control in a warehouse?
An SOP (or “standard operating procedure”) for quality control in a warehouse is a set of instructions outlining the steps that each team member must follow when performing a warehousing activity (such as receiving, putaway, picking, or packing) to ensure quality and consistency in the warehouse.