Table of Contents
** Minutes
What is work in process inventory?
Formula to calculate work in process inventory
Accounting for WIP inventory in the balance sheet
3 metrics you need to know to calculate current WIP inventory
How to optimize work in process inventory flow
Many products are made up of several components that must be made or purchased before people making the product can use them to manufacture the final product. For example, think of a computer mouse: it looks like a simple device, but if you take it apart, you will find several different pieces that make the mouse function as it should.
The cost of purchasing a product factors into what it costs to make it (e.g., raw materials, labor, and production). Thus, your ending WIP inventory is essential to know for inventory accounting.
In this article, you’ll learn what costs are associated with work-in-process (WIP) inventory and how to determine how much WIP inventory you have in production.
What is work in process inventory?
Work in process (WIP) inventory is a term used to refer to partly finished materials within any production round. Work in process in production and supply chain management refers to the total cost of unfinished goods currently in production.
Any raw material inventory that humans have worked on but is not yet considered a finished good is a work-in-process inventory. You can think of WIP inventory as all inventory that has not yet reached the finished product inventory but is not raw materials. This makes WIP inventory a part of manufacturing inventory.
Businesses that sell highly custom products (e.g., hand-made products on Etsy) are more likely to oversee the WIP inventory process than a business that purchases finished goods directly from a supplier or manufacturer.
Formula to calculate work in process inventory
The work in process inventory formula consists of the ending work inventory for that period, and the beginning work inventory for the next one. Once you’ve determined your beginning WIP inventory and you calculate your manufacturing costs as well as your cost of manufactured goods, you can easily determine how much WIP inventory you have.
The formula for calculating WIP inventory is:
Beginning WIP Inventory + Manufacturing Costs – COGM = Ending WIP Inventory
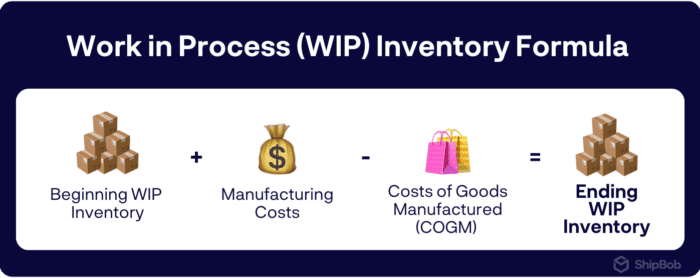
Calculating WIP inventory examples
To help you better understand how to determine the current WIP inventory in production, here are some examples.
WIP inventory example #1
Let’s say your company’s beginning WIP, as determined by the previous accounting record, is around $10,000 for the new year. During the new year, your business spends $150,000 on manufacturing costs. Furthermore, your total cost of finished goods is $250,000. This leaves your ending WIP inventory as:
Beginning WIP Inventory + Manufacturing Costs – COGM = Ending WIP Inventory
$110,000 + $150,000 – $250,000 = $10,000.
So, your ending work in process inventory is $10,000.
WIP inventory example #2
For a more comprehensive example, let’s say you run a shoe brand with a beginning WIP of $100,000. In the new year, you spend $150,000 on manufacturing costs. Your manufacturer also produced 5,000 pairs of shoes, each costing around $30 to produce on average. Your cost of finished goods is:
$30 x 5000 = $150,000
From there, you would calculate the ending WIP inventory amount:
Beginning WIP Inventory + Manufacturing Costs – COGM = Ending WIP Inventory
$100,000 + $150,000 – $150,000 = $100,000
Thus, your ending WIP inventory comes out to be $100,000 for the year.
Accounting for WIP inventory in the balance sheet
Similarly to inventory and raw materials, the WIP inventory is accounted for as an asset in the balance sheet. All costs related to the WIP inventory, including the costs of raw materials, overhead costs, and labor costs, need to be considered for the balance sheet to be accurate.
Usually, accountants assign all raw materials, gather all labor and overhead costs, and then record the sum of all these costs as an asset entry in the balance sheet. Consider the example below.
Date | Description | Debit | Credit |
---|---|---|---|
1/5/24 | Purchase raw materials | Raw materials $5,000 | Accounts payable – $5,000 |
5/5/24 | Move raw materials to WIP | WIP inventory – $5,000 | Raw materials – $5,000 |
5/10/24 | Add labor & overhead to WIP | WIP inventory – $3,000 | Wages – $3,000, Manufacturing – $1,000 |
5/15/24 | Transfer to finished goods | Finished goods inventory – $6,000 | WIP inventory – $6,000 |
5/20/24 | Sell finished goods (revenue) | Accounts receivable – $10,000 | Sales revenue – $10,000 |
5/20/24 | Sell finished goods (COGS) | Cost of goods sold – $6,000 | Finished goods inventory – $6,000 |
3 metrics you need to know to calculate current WIP inventory
The cost of WIP inventory is a bit more complex than determining the value of finished goods, as there are many more moving parts. Before attempting to calculate your current WIP inventory value, here are some terms you will need to know first.
1. Beginning work in process inventory cost
The beginning WIP inventory cost refers to the previous accounting period’s asset section of the balance sheet. To calculate the beginning WIP inventory, determine the ending WIPs inventory from the previous period and carry it over as the beginning figure for the new financial period.
2. Manufacturing costs
Your manufacturing process costs refer to all costs associated with manufacturing a finished product. This includes the cost of raw materials (or production inventory), labor, and overhead costs. The more WIP inventory that goes through the production process, the higher the raw materials and labor costs will be, which will impact the total costs of manufactured goods. The formula is:
Raw Materials + Direct Labor Costs + Manufacturing Overhead = Manufacturing Costs
3. Cost of manufactured goods
Cost of manufactured goods (COGM) refers to the total costs incurred to make a final product. You will need to know the final COGM to calculate the value of your current WIP inventory value. COGM is determined by adding the total manufacturing costs with your beginning WIP inventory. From there, you subtract the ending WIP inventory, which will give you the total cost of manufactured goods. The formula is:
Total Manufacturing Costs + Beginning WIP Inventory – Ending WIP Inventory = COGM
How to optimize work in process inventory flow
Most ecommerce businesses rely on a supplier or manufacturer for sellable inventory. The process and flow of WIP inventory are important to understand because they can indicate how efficient your supplier or manufacturer is at producing finished goods. By working closely with your supplier and other partners in your retail supply chain, like a 3PL company, you can find ways to optimize the supply chain.
1. Source the right supplier
Unless you sell a highly customizable product, you likely won’t have much visibility into the process of WIP inventory. You do have control over product sourcing and the manufacturer you choose to work with, and it’s up to your manufacturer to keep track of WIP levels and find ways to reduce costs while optimizing their labor, workforce, and production processes. But you can ask your supplier questions like:
- Where are the raw materials coming from?
- Is there a way to cut costs and production lead times?
- Can your goods be made closer to home?
2. Use a 3PL to help with inventory management
Inventory is often the biggest asset of an ecommerce business. Once your WIP inventory turns into sellable goods, you will need a system in place to track inventory as it’s being sold. ShipBob’s technology fully integrates with your store to easily manage all inventory and orders from one central dashboard while they fulfill your orders on your behalf.
By partnering with a third-party logistics (3PL) company like ShipBob, you can manage inventory in real-time, view beginning inventory numbers and inventory days on hand, access demand forecasting tools, get insights into inventory turnover, and more.
Optimize your work-in-process inventory with ShipBob
Understanding WIP inventory can help you better understand supply chain management, so you can find ways to optimize your supply chain to drive more revenue.
Managing inventory is a significant part of growing a successful online store. If you need help with warehousing and fulfillment, be sure to partner with a fulfillment provider that has the services, technology, data and analytics, and expertise you need to help you make better business decisions and keep customers happy.
Inventory analytics dashboard
With ShipBob’s best-in-class inventory management software, brands can closely monitor inventory. Our data and analytics dashboard is equipped with data to help your brand track inventory levels, fine-tune demand forecasting, set reorder points, and help you make better inventory decisions.
Technology-driven fulfillment solutions
Brands in the US can leverage ShipBob’s Inventory Placement Program (IPP) to speed up transit times and lower shipping costs. IPP automatically distributes and places inventory throughout the US and fulfills orders from the fulfillment center closest to the end customer.
“
IPP has been a game changer for us. First, it reduces costs for us, because we’re shipping more orders a much shorter distance. Second, and maybe equally as important, it’s reducing the time that customers have to wait to get packages.Tyler McCann, Co-Founder of Taste Salud
Maybe outsourcing order fulfillment isn’t an option for your business. ShipBob offers its proprietary warehouse management system, or WMS, (the same one used in all 50+ of our fulfillment centers) to brands that operate their own warehouse. ShipBob WMS’s intuitive interface allows brands to optimize and streamline order fulfillment by improving inventory management, boosting order accuracy, and more.
“One of the biggest reasons we went with ShipBob is the multiple checks from start to finish. The WMS makes it really hard to send out the wrong product. It still happens on rare occasions – but it happens a lot less than before. Before we implemented ShipBob’s WMS, our order accuracy rate was around 92%. Now we’re at 99.7% for order accuracy, which equates to 2,100 less mispicks a year on average.”
Jourdan Davis, Operations Manager at Pit Viper
Custom packaging and kitting
ShipBob’s Customization Suite has multiple high-quality features to enhance the unboxing experience. With full-color, customizable gift notes and marketing inserts, brands can make gift-giving extra special and boost customer loyalty and satisfaction.
Additionally, ShipBob offers kitting and custom packaging to help extend your brand experience from online shopping through unboxing.
Customized and scalable solutions
Brands of all sizes and stages can unlock scalable fulfillment solutions with ShipBob. From our Growth Plan to global fulfillment capabilities and B2B offerings, ShipBob can help brands reach their goals and continue to grow their business.
To learn more about how ShipBob helps ecommerce businesses, contact us by clicking the button below to start the conversation and get pricing.
Work in process inventory FAQs
Understanding WIP inventory can be challenging, especially since it consists of many moving parts during the production process. Here are some common questions that companies have on WIP inventory.
Why is work-in-process inventory important?
Knowing how to accurately calculate WIP inventory can impact your balance sheet. If your business offers highly customized products, then it’s important to understand how WIP inventory works, what goes into the cost, and how to calculate it at the end of the accounting period. This will give you a sense of COGS based on how much it costs to produce and manufacture finished goods.
What is the difference between ‘work in process’ and ‘work in progress inventory?’
‘Work in process’ typically describes raw materials that are converted into finished goods inventory over a relatively short duration of time.
On the other hand, ‘work in progress’ is often used in construction and other service businesses and refers to the progress of a project and how much it costs compared to the percentage of completion.
When these terms are used by businesses selling a physical product, both mean the same thing.
What is the difference between WIP inventory and finished goods inventory?
‘Work in process’ inventory refers to unfinished products that are somewhere in the manufacturing process, and are therefore unsellable.
‘Finished goods’ inventory are items that have been completed by the manufacturer and are ready to be sold for revenue.