Table of Contents
** Minutes
What is finished goods inventory?
How to calculate finished goods inventory in 4 steps (formula + example)
Why is the finished goods inventory formula so important?
How logistics partners like ShipBob help improve finished goods inventory management
Managing inventory is one of the most demanding parts of running an ecommerce business. With so many moving parts, it can be difficult to keep track of all the inventory available for customers—especially as you expand into multichannel inventory management.
If you have inventory split across multiple fulfilment centres, inventory tracking becomes even more complicated. You have to account for inventory that’s currently going through the manufacturing process, in transit, and that’s readily available for purchase. It’s not easy to stay on top of, but there are ways to make inventory management easier.
One ‘tool’ used by ecommerce businesses is the finished goods inventory formula. By knowing the amount of finished inventory on hand, your small business can accurately determine stock levels for improved inventory tracking.
What is finished goods inventory?
Finished goods inventory is the total stock available for customers to purchase that can be fulfilled. Using the finished goods inventory formula, sellers can calculate the value of their goods for sale.
‘Finished goods’ is a relative term, as a seller’s finished goods may become a buyer’s raw materials. For example, a textile factory may produce materials that can be used in clothing, such as cotton or silk. While the cotton or silk may be the textile factory’s finished goods, they can sell them as raw materials to apparel retailers who will create them into new finished goods: clothing.
Finished goods inventory abbreviations cheat sheet
Feeling lost? Here’s a quick guide to the term abbreviations we’ll use in our finished goods inventory calculations:
- COGM: Cost of goods manufactured
- COGS: Cost of goods sold
- WIP: Work-in-process
How to calculate finished goods inventory in 4 steps (formula + example)
The formula to calculate finished goods inventory is as follows:
Finished Goods Inventory Formula = (COGM – COGS) + Value of Previous Year’s Finished Goods
To use this formula, you’ll first need to calculate your cost of goods manufactured (COGM) and cost of goods sold (COGS). Here is how to calculate both figures:
COGM = (Beginning WIP Inventory + Total Manufacturing Cost) – Ending WIP Inventory
COGS = (Beginning Inventory + Purchases During the Period) − Ending Inventory
Note: You will want the accounting period to be consistent throughout these formulas.
Let’s go over a quick step-by-step example of how to calculate finished goods inventory using all three formulas.
Say your brand makes and sells candles, and you want to calculate your finished goods inventory.
Step 1: Decide the time period.
For the sake of accuracy, you’ll need to work with the same time period for all of your formulas.
Say you run an ecommerce business that makes and sells candles, and you want to calculate your finished goods inventory.
Your first step would be to decide on a time frame for your calculations. For instance, you decide that you want to figure out what your finished goods inventory was last quarter.
Step 2: Gather the necessary data.
Next, you should gather all the information you will need to use the 3 formulas. In our example, we’ll assume that you comb your business’s records and find that:
- Beginning WIP Inventory = $750
- Ending WIP Inventory = $175
- Total Manufacturing Cost = $425
- Beginning Inventory = $250
- Ending Inventory = $200
- Purchases During the Period = $550
- Value of Previous Year’s Finished Goods = $100
Step 3: Calculate COGM and COGS.
Next, plug the appropriate data into the formulas for COGM, like so:
COGM = (Beginning WIP Inventory + Total Manufacturing Cost) – Ending WIP Inventory
COGM = ($750 + $425) – $175
COGM = $1,175 – $175
COGM = $1,000
Do the same to calculate COGS:
COGS = (Beginning Inventory + Purchases During the Period) − Ending Inventory
COGS = ($250 + $550) – $200
COGS = $800 – $200
COGS = $600
Step 4: Calculate finished goods inventory.
Finally, plug the COGM and COGS results and the data for the value of the previous time period’s finished goods into the formula for finished goods inventory, like so:
Finished Goods Inventory Formula = (COGM – COGS) + Value of Previous Year’s Finished Goods
Finished Goods Inventory Formula = ($1,000 – $600) + $100
Finished Goods Inventory Formula = $400 + $100
Finished Goods Inventory Formula = $500
In our example, your company’s finished goods inventory for the last quarter would be $500.
Why is the finished goods inventory formula so important?
Calculating good inventory formula can benefit your brand in many ways. Here’s how the finished goods inventory formula can help your business.
Improves financial budgeting
Balance sheets, financial statements, income statements, and other financial documents must account for current assets — inventory being your biggest one. When you know your finished goods inventory value, you are in a better position to report accurate financials and create operating budgets for the present and future.
Records the number of current assets
Even one mistake in your inventory accounting process can lead to an IRS audit. With the finished goods formula, you can easily track work-in-process (WIP) inventory, production inventory, and unfinished goods to ensure your accounting is accurate.
Reduces waste of materials
Knowing the optimal inventory levels for your business can save you money in the long run. Instead of spending a lot of money on warehousing an excessive amount of raw materials inventory and finished products, you can save by storing only what’s needed.
Optimizes inventory management processes
Supply chain optimizations can always be made through automation or labour efficiency. By knowing the finished goods formula, you’ll be able to track direct labour costs and manufacturing costs to find opportunities to improve production processes and automation opportunities.
Minimizes stockouts
Out-of-stock products and backorders cause customers to wait a long time for their purchase until an item is back in stock or cancel the order altogether. With the finished goods inventory formula, you can accurately predict how much inventory is needed to prevent stockouts.
How logistics partners like ShipBob help improve finished goods inventory management
Constantly calculating COGM, COGS, and finished goods inventory is a hassle. As a result, many ecommerce businesses outsource fulfilment and inventory storage to 3PLs (or third-party logistics providers).
Logistics partners not only provide professional order fulfilment services, but make inventory auditing and management easier by leveraging inventory management software that tracks and records data for you.
Here’s a deeper look into how an ecommerce enablement partner like ShipBob can help you optimise your inventory management.
1. Track inventory levels in real-time
Tracking all your inventory by hand may be feasible if you’re only selling a few SKUs SKUs or fulfilling a few orders per month – but as your business grows, you’ll need a scalable, automated way to monitor inventory levels.
ShipBob’s dashboard enables business owners to see their inventory levels across storage locations and sales channels in real-time. You can also access up-to-date analytics to track SKU velocity, days on hand, average units sold per day, storage costs, and other inventory metrics to deliver more actionable insights.
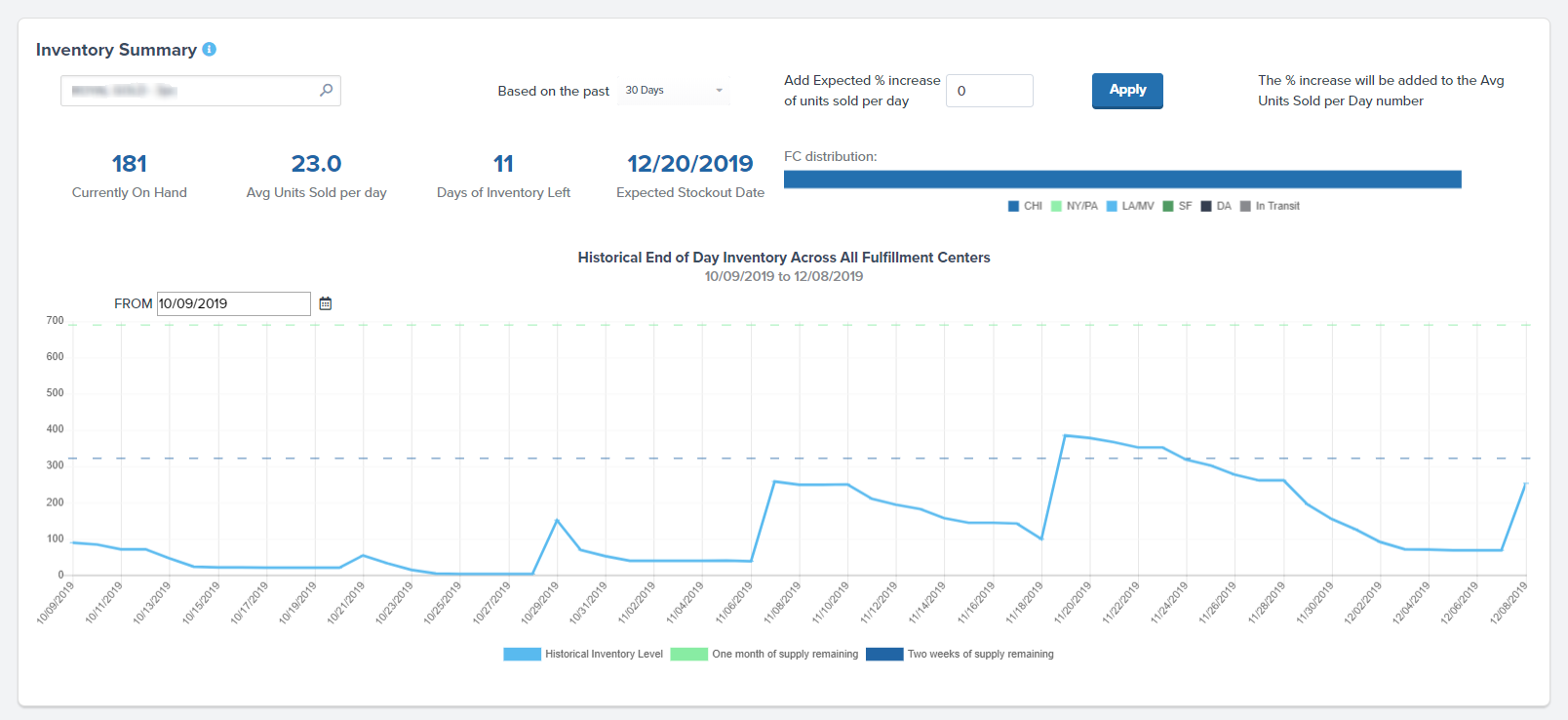
2. Automate reorder notifications to prevent stockouts
If you forget to replenish inventory at the right time, you may not have enough stock left to meet demand. This can cause stockouts and backorders, which are never popular with customers.
Through ShipBob’s dashboard, you can set and receive automatic reorder point notifications for each SKU. That way, when that SKU’s quantity falls below a specific threshold, you can reorder on time and never lose sales to stockouts.
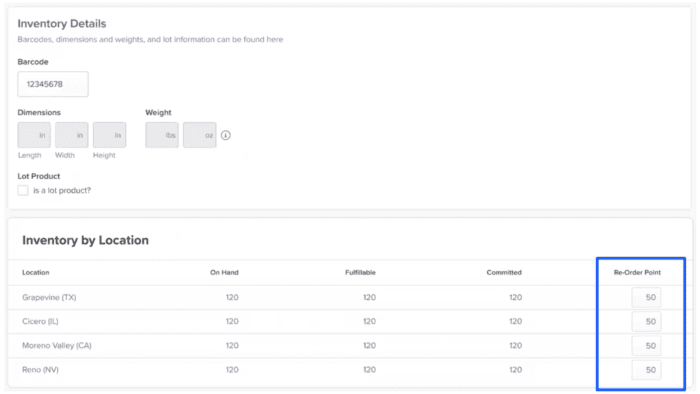
3. Forecast demand more accurately
ShipBob’s analytics tool makes it easy to find the data your brand needs to make important decisions. You can analyse each SKU’s performance and calculate inventory turnover to distinguish your best-sellers from your slow-movers, and leverage the historical order data that ShipBob automatically tracks for your brand to achieve more accurate trend and demand forecasts. With this data, you’ll have a better understanding of what to stock when.

4. Distribute inventory strategically
As your brand continues to grow, you may end up having to split inventory across multiple fulfilment centres to reach distant customers more quickly and affordably.
Using ShipBob’s Ideal Inventory Distribution tool, ShipBob customers can calculate the optimal allocation of inventory across ShipBob’s fulfilment centre network based on past order destinations. This enables you to reduce the average shipping zone you ship to, minimising shipping distances and costs.
Merchants can even leverage ShipBob’s Inventory Placement Program to have ShipBob physically distribute their inventory for them. All you have to do is send inventory to one of ShipBob’s hub locations, and ShipBob will take care of the rest.
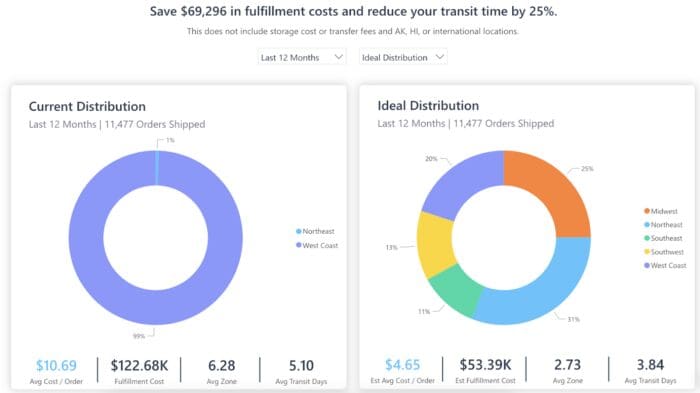
How ShipBob’s inventory management expertise helped ZBiotics streamline inventory
When it comes to managing your inventory, your brand needs a partner that can deliver cutting-edge, effective solutions.
Probiotic drink brand Zbiotics discovered this when they transitioned to a fulfilment partner with archaic technology. After dealing with a dashboard that lacked many core functionalities, they decided to partner with ShipBob and access the high-quality software they needed.
Zbiotics soon joined ShipBob’s Inventory Placement Program, and were able to distribute their inventory across 4 ShipBob fulfilment centres. This not only saved them time and effort, but also helps them get their products to customers faster.
“Before being a part of the Inventory Placement Program, we were shipping LTLs to each fulfilment centre, so it made a lot of sense for us to take advantage of this program. Previously, our Inventory Planner was doing calculations to determine which SKUs needed to go where, but she doesn’t have to do that now. This solution has made our jobs easier, and the pricing was competitive.
There’s a level of visibility that allows us to see the internal transfers being made, so we know when products are expected to arrive at each fulfilment centre. While I love working within spreadsheets, that type of modeling is rough because it isn’t updated in real-time. Using ShipBob’s real-time data and being able to see when inventory reaches the initial hub location really takes work off of our plates.”
Michael Mullaney, VP of Supply Chain at ZBiotics
To learn more about how ShipBob can help with inventory optimisation and ecommerce fulfilment, click the button below to contact us and request a pricing quote.
Finished goods inventory FAQs
Here are answers to some of the most common questions about finished goods inventory.
What type of account is finished goods inventory?
Finished goods inventory should be listed as one of your short-term assets on your company’s balance sheet.
How do you record finished goods inventory?
You can record finished goods inventory on your balance sheet as a current asset. You should also track and record finished goods inventory value over time in a separate capacity.
What is the difference between work-in-progress and finished goods inventory?
There are different types of inventory. Work-in-process inventory refers to the total amount of inventory that is partly finished within any production round, or inventory that is still in the process of being created or completed.
Finished goods inventory, in contrast, is the total amount of final product, or inventory that is complete and sellable.
How does finished goods inventory affect a company’s financial statements?
Finished goods inventory are usually a positive thing to see on a company’s financial statements and balance sheets, as they are counted as an asset and therefore bring value to the company. This value often depends on the accounting methods a brand uses to calculate COGS (and, by extension, finished goods inventory).
What are examples of finished goods?
Finished goods are any products that are in their final state and available to be sold.
The table below compares goods considered WIP inventory and finished goods.
WIP Inventory | Finished Goods |
A half-knitted sweater | A completed sweater |
An unbound book | A bound book |
Cereal | Cereal sealed in a cereal box |