Table of Contents
** Minutes
Common causes of warehouse overflow
Challenges of managing warehouse overflow
Preventative strategies to avoid warehouse overflow
A well-stocked warehouse is every ecommerce business owner’s dream; an overstocked warehouse, on the other hand, is a logistical nightmare. Whether it’s because of a miscalculation, capacity constraints, unexpected demand shifts, or just bad luck, warehouse overflow presents a number of challenges for ecommerce businesses.
In this post, we’ll break down the common causes of warehouse overflow, share some best practices for preventing it, and how experts like ShipBob can help you manage your inventory and storage.
What is warehouse overflow?
Warehouse overflow occurs when your inventory levels exceed your maximum warehouse capacity.
In other words, warehouse overflow happens when you have too much excess inventory, to the point where you can’t store it all in your current warehouse space. This excess could result from:
- Supplier or manufacturer error
- Inventory obsoletion
- Inaccurate demand forecasting
- Unexpected demand shifts
- Supply chain disruptions or bottlenecks
Whatever the root cause, warehouse overflow often leads to warehouse congestion and disorganisation, both of which present safety hazards and can lower your operational efficiency.
The impact of warehouse overflow on business operations
To get an even better understanding of why warehouse overflow is such a major concern for ecommerce businesses, let’s take a look at how it impacts your operations.
Increased storage costs
When you’re trying to store more inventory than your warehouse space can hold, it won’t just be physically cramped; it’s also going to increase your inventory carrying costs. The more inventory you have, the more space it takes up – and since storage fees are usually charged per bin, per pallet, or per shelf, warehouse overflow naturally raises your storage costs.
Even if you’re running your own warehouse, warehouse overflow may force you to spend more money on storage infrastructure. The cost of procuring additional shelves, bins, and pallets to accommodate the inventory overflow can add up to impact your overall storage costs.
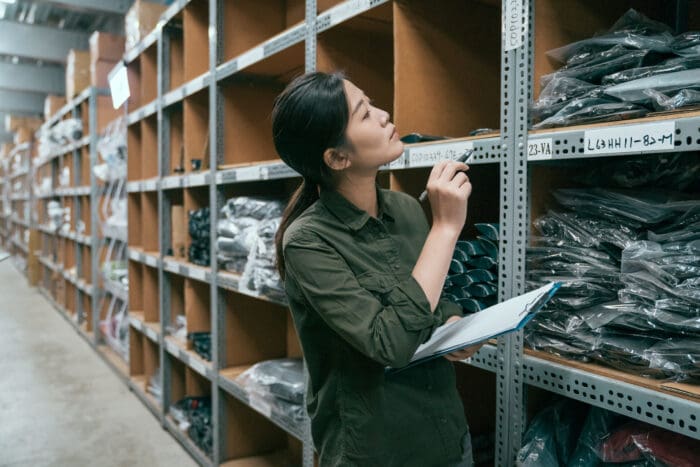
Delayed shipments
Overflow can lead to disorganization and warehouse congestion, which could make it more difficult for your warehouse staff to find and pick items needed for fulfilment. This slows the entire order fulfilment process, which in turn lengthens lead times, delays delivery, and ultimately negatively impacts customer satisfaction.
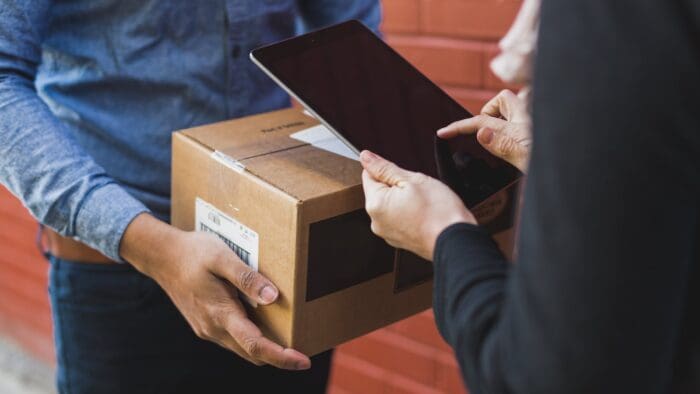
Reduced operational efficiency
With inventory spilling over its allotted warehouse space, your staff will experience challenges navigating and moving across the warehouse. It becomes difficult to seamlessly move between smaller aisles and overloaded shelves without posing a risk to warehouse safety. This prevents workers from efficiently performing their tasks, which directly impacts your logistics efficiency.

Common causes of warehouse overflow
Lots of different factors can lead to warehouse overflow. Here are some of the most common reasons why ecommerce businesses may experience overflow problems.
High seasonal demand
Demand typically spikes during peak seasons, which means businesses tend to stock up to meet this increased demand. However, as peak shipping season ends, they may not always sell off their seasonal stock. This excess inventory takes up valuable space and limits your storage capacity, contributing to overflow.
ShipBob has proved that they can weather sudden and intense spikes in demand without compromising on fulfilment speed or quality. ShipBob’s ability to staff appropriately as demand ebbs and flows has been a huge advantage for us, especially during peak. It makes our lives so much easier, and we don’t have to worry about handling it ourselves.”
Molly Noonan, Senior Manager, Supply Chain at Tonies
Inaccurate forecasting
A common culprit of overflow inventory is inaccurate demand forecasting. If you overestimate how much demand you’ll see for a certain product and you end up selling much less inventory than you’d originally anticipated, the unsold inventory turns into deadstock. When this happens repeatedly, it can reduce your available storage space and lead to overflow.
Limited storage space
For some brands, the problem is not that they have too much inventory; they just have too little space. If you know you ordered the right amount of stock to meet demand but are still dealing with overflow issues, it’s probably time to think about expanding capacity.
That said, sometimes brands experience overflow because they aren’t making the best use of their physical space. For instance, a business might run out of storage space on warehouse floors, but not realise there’s plenty of free vertical space that they could use by installing warehouse racks. Warehouse slotting solutions allow them to make use of all available space in the warehouse and increase capacity.
Business growth outpacing infrastructure
While every business strives for growth, its existing infrastructure may not be able to support said growth. If you’re stocking up on more inventory to meet growing customer demands but still rely on the same storage facilities that you used when you started out, chances are you’ll run into overflow problems.
“Customers love the delivery experience we’ve built with ShipBob, and it shows. When we first launched with ShipBob in the UK, we had a relatively conservative order volume estimate of a few thousand orders per month. But within just 4 months, we were receiving over 30,000 orders per month. It all just worked seamlessly.”
Kevin Lammers, International Business Manager at TopBuxus
Check out ShipBob's Warehouse Management System (WMS)
ShipBob's WMS helps your warehouse reduce picking errors, manage inventory in real time, and fulfill orders faster.
Challenges of managing warehouse overflow
While warehouse overflow won’t doom your business, it does present several challenges that can be costly and time-consuming to overcome.
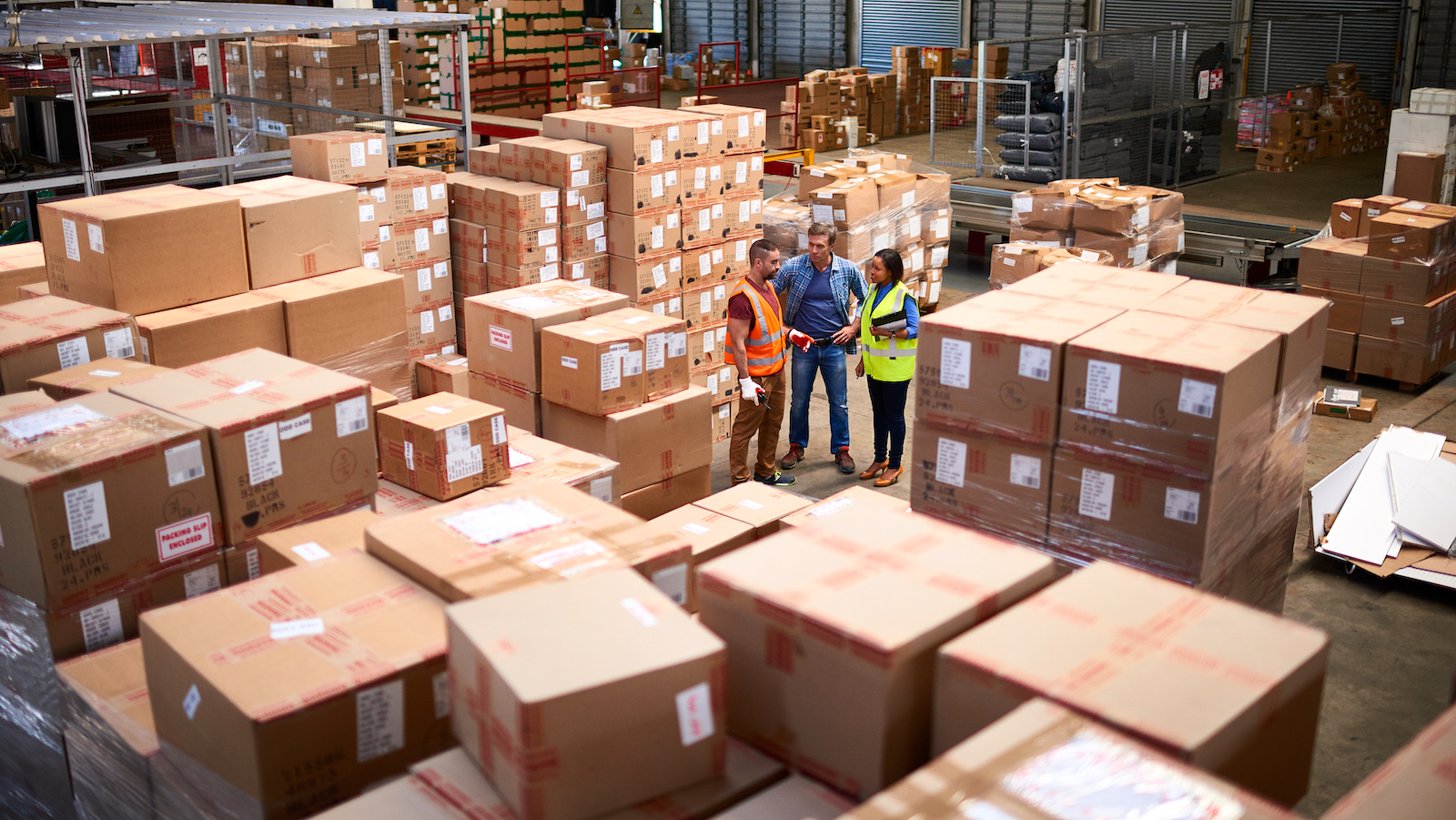
Disorganised inventory
If your racks and shelves are already full, there’s no place to store additional incoming inventory during the warehouse putaway process. This leads to disorganisation, which will negatively impact your warehouse inventory management.
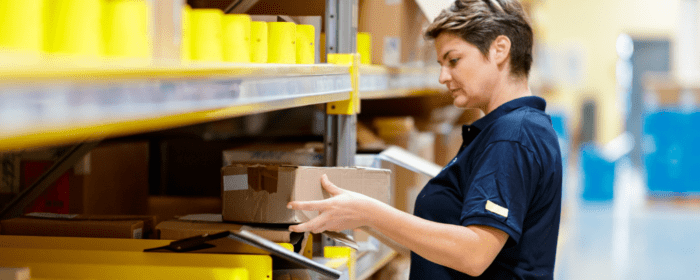
Delayed order picking
In a disorganised warehouse, it’s much easier for items to get stored in the wrong places. This slows down your warehouse picking process, as your fulfilment staff may have a harder time locating the items they need – and when they do locate the items, retrieving them may be difficult if the warehouse is congested.
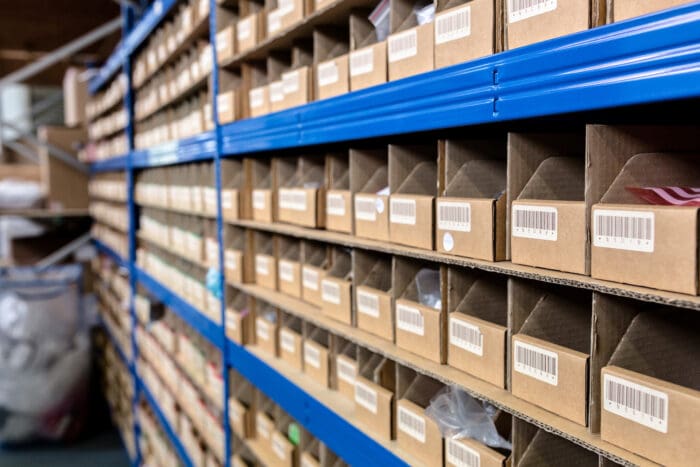
Temporary storage solution costs
Even if a business makes use of on-demand warehousing for overflow storage, this type of temporary storage solution is unsustainable. The high costs of leveraging these short-term solutions will eventually add up to eat away at your bottom line – not to mention that there’s no guarantee the warehouse will support your needs during peak seasons.
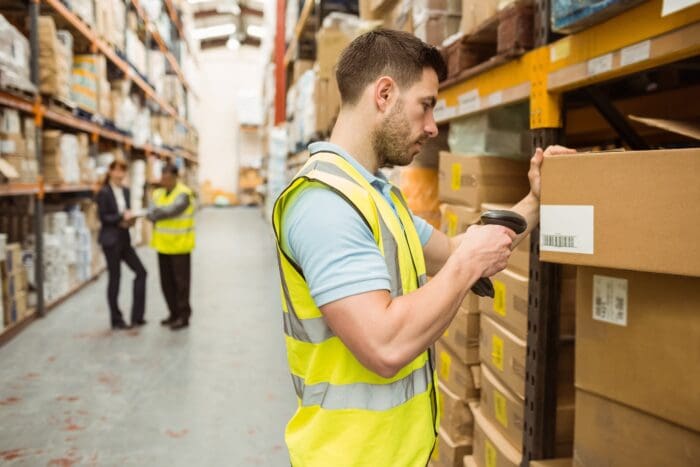
Health and safety hazards
Warehouse overflow can very easily lead to warehouse congestion. In a congested warehouse, racks and shelves may be overloaded, which could collapse and threaten worker safety. Congested aisles also pose a risk of accidents and collisions.
Additionally, boxes stored on the floor may become a tripping hazard. Meanwhile, congestion also prevents accurate inventory tracking, which means that some items may expire, leak, or spill, which may threaten the health and safety of your warehouse staff.
Preventative strategies to avoid warehouse overflow
The best way to manage warehouse overflow is to prevent it from occurring in the first place. Here are some of the best preventative strategies to avoid and reduce overflow issues.
Optimise your warehouse layout
To boost warehouse capacity and avoid overflow, try assessing and improving your warehouse layout. Optimise your warehouse setup to maximise your available storage areas, and consider investing in shelving systems that will help you make the most of any vertical space. You can even look for ways to reorder shelves and storage to hold more inventory (and even make picking more efficient).
Invest in real-time inventory management
Having real-time inventory visibility is crucial to get a realistic understanding of your actual inventory needs. When you can see exactly how much stock you have, it’s easier to plan your replenishment order so that you’re not reordering more inventory when you already have sufficient stock.
A top-notch warehouse management system (WMS) or inventory management system can deliver this level of visibility and help you monitor inventory levels. For instance, ShipBob’s WMS features built-in inventory management capabilities – including real-time inventory tracking and automatic reorder notifications – which you can leverage to accurately plan your procurement and avoid overstocking.
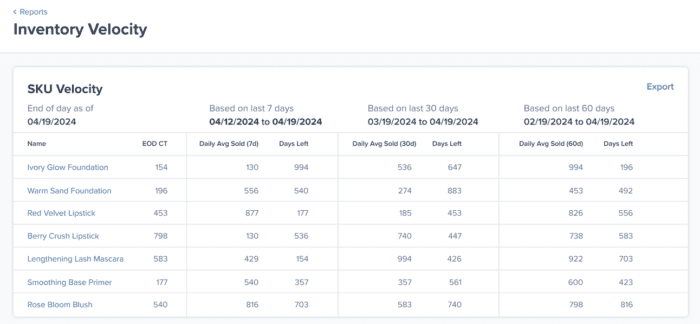
Learn demand forecasting and inventory placement
While your current stock levels give you some idea of your inventory needs, it’s only one side of the coin. To get an even more precise understanding of how to plan your replenishment orders, you need accurate demand forecasting.
To forecast demand correctly (and avoid overstocking), look at your brand’s sales history, inventory performance, and any current demand trends. In addition, consider where your customers are and what locations are seeing the most demand for which products. Armed with this information, you will be in a better position to predict demand and allocate inventory accordingly.
Solve overflow with ShipBob’s warehousing solutions
Whether you’re looking for more storage space, better inventory management, or even to outsource warehousing altogether, ShipBob can help. As an expert supply chain and fulfilment partner, ShipBob optimises inventory storage and management for thousands of ecommerce brands to minimise costs while maximising efficiency.
Here are just some of the ways that ShipBob’s solutions can help you avoid warehouse overflow, plus streamline your inventory and ecommerce warehousing operations as a whole.
Outsource overflow to ShipBob’s fulfilment network
ShipBob offers scalable solutions to warehouse overflow that help you store and manage large amounts of inventory. With 50+ fulfilment centres across the globe, you can strategically distribute your inventory to avoid overflow at any one location, equip each fulfilment centre to meet demand, and even improve shipping speeds.
Get on-demand storage flexibility
ShipBob’s flexible storage solutions give you the flexibility to scale up or down as you need. This can support your holiday inventory preparation, helping you effectively handle increased demand during peak shopping seasons with the freedom to scale down during slower months.
To learn more about how ShipBob can help you manage your inventory, click the button below to get in touch with an expert.
Warehouse overflow FAQs
Below are answers to the most commonly asked questions about warehouse overflow.
What are the best practices for managing warehouse overflow during peak seasons?
Some best practices for managing warehouse overflow during peak seasons include:
- Reworking your warehouse layout to maximise existing storage space (including vertical space)
- Conducting an inventory audit to move out deadstock and obsolete inventory
- Outsourcing fulfilment and storage to a flexible warehousing and fulfilment provider that offers dynamic storage solutions
Can ShipBob’s fulfilment network reduce my warehousing costs?
ShipBob’s fulfilment network can help reduce your warehousing costs. By strategically distributing your inventory across multiple of ShipBob’s facilities, you can minimise the high holding costs that result from warehouse overflow and reduce your shipping costs by placing inventory closer to customers.
What are the risks of not managing warehouse overflow?
Not managing warehouse overflow leads to warehouse congestion and disorganization, which can slow down your operations, increase safety risks, and delay shipments.
What is an overflow warehouse?
An overflow warehouse is a backup storage facility that a business uses to store inventory when the primary warehouse reaches capacity.